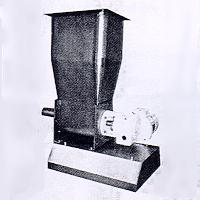
Acromet 1000 feeders are designed and manufactured for durability in service and long term dependability in feeding with consistent accuracy. Acromet volumetric feeder and gravimetric systems are successfully used in feeding materials in many forms: powders, granules, pellets, chips, chunks, and flakes. Satisfaction is assured with the Acromet 1000. All forms of product flow and handling characteristics can be accommodated by the selection of the appropriate model and optional features developed by Acromet over the years, including where required the use of automatic control instrumentation, to ensure the maintenance of flow rates in line with demand to meet process requirements.
Specifications
- CO-AX feeding system + duo drive = winning combination
- CO-AX + DUO-DRIVE = the winning combination for volumetric or gravimetric control
- Feed rates:
- Model 1200: 0.002 to 0.4m^3 / hr
- Model 1500X / Z: 0.002 to 6m^3 / hr
- Model 1700: 0.4 to 100m^3 / hr
Features
- CO-AX a coaxal multi-function system compromising product flow inducer, low speed pre-feed bulk density blender and metering system.
- The co-ax system provides:
- A continuous product flow from hopper to feed chamber.
- B gentle coaxal pre-feed conditioning / blending to ensure constant bulk density of product in the flow tube.
- A pre-requisite of feeding accuracy
- C uniformity of flow rate either simplex or duplex or auger system through product flow tube.
- A + B + C = gravimetrically uniform discharge:
- No vibration - no aeration - no product compaction by flexing diaphragms or twisting hoppers.
- No flow rate irregularities.
- DUO-DRIVE: the Acromet unique integral gear combination:
- Facilitates low speed product conditioning / density with higher speed feed augers.
- Facilitates coaxal blending thus uniform bulk density of product around and in the fed auger.
- Represents a compact - easily cleaned design - no belts, chains or exposed moving parts - single flange mounted motor - no insanitary cosmetic panelling - light weight.
- Robust construction:
- ACROMET 1000 feeders are designed and built to last.
- ACROMET's combination of integral gear drive, self lubricating seals and rigid hopper design means that long life and reliability are a reality.
- Custom design capability:
- ACROMET successfully feeds products that have defeated others.
- ACROMET's test laboratory experience has encompassed all sorts of materials that sticks, hang up, arch, rat hole or worse. With an experimental emphasis on pre-feed conditioning techniques, ACROMET has extended the realms of the "possible".
- All new designs are proven by thorough in-house or on site testing before final release. In addition, the inherent design flexibility of the ACROMET feeder allows modifications in the event of changes to the material or feed rates.
- Quality assurance: ACROMET is committed to total quality management in accordance with AS3902 / ISO9002. In support of that commitment and in addition to our extensive warranties, product service facilities and provision for ready and ongoing availability of parts, we offer an ACROMET product application engineering service designed to ensure total satisfaction.
- Applications: food products, chemicals, plastics, pharmaceuticals, water treatment additives, building and industrial products.
- Industrial durability-laboratory accuracy / accuracy:
- +/-0.5% (total deviation) achievable with Acromet volumetric feeder when others fail. This is made possible with the unique co-axal system delivering grammatically uniform products to the feed mechanism.
- Anything less than the Acormet's co-axal system of material pre-conditioning involves intermittent manipulations of material by hopper diaphragms and the like, causing undesirable product density inconsistency and variations in gravimetric feed rate.
- Applications experience: Acromet's accumulated experience in the feeding of dry materials of more than 30 years is reflected in the development of feeders that regularly perform the impossible: by providing reliable and economical solutions.
- Testing: tests are conducted in Acromet's test facilities where samples of any material can be used to demonstrate feed accuracy attainable with the various models, pre-conditioning and feeding elements. Hire units are available for on site testing of hazardous products.
- Feed chambers and hoppers: Acromet 1000 dry material feeders are designed and constructed for long term industrial applications. Hoppers and feed chambers are produced in mild steel and stainless steel (to food standard finish as required).
- Self adjusting seals: the Acromet PTEE packed drive shaft seal is self lubricating and self adjusting. Perodic adjustment is not required.
- Metering auger:
- The metering auger runs in the centre of the material pre-conditioning zone in the feed chamber thus conveying material of uniform bulk density: a prerequisite for accuracy.
- Augers are manufactured in stainless steel and in a number of designs, the selection of which for any application is dependant on the characteristics of the product and required flow rates.
- Material conditioning: a variety of material pre-conditioning mechanisms is used - as required by materials of differing characteristics - to establish gravimetric uniformity of the material as it enters the feed tube and thus consistent rates of material discharge.
- Duo drive:
- The Acromet unique concentric drive combination gearbox facilitates the low speed rotation of product conditioning elements - for gentle product handling - while higher speeds are used on the feed auger to provide a more continuous discharge of product.
- All gearbox components are heavy duty with a substantial safety margin to cope with any "unplanned" stress arising from off specification material entering the feed chamber.
- A twenty year service life can be anticipated under normal operating conditions and proper service.
- Motor drive: manual and automatic control systems can be provided. AC and DC automatic variable speed units are available which will accept a 4-20mA control signal for incorporation in process control systems.
- Gravimetric control systems:
- Gravimetric control, whether incorporating the weighing of belts, augers or hoppers, requires - to achieve the best from the investment in the equipment - the uniform discharge of material from the feeder.
- Erratic delivery, caused by intermittent use of secondary flow promoting devices such as air blasts, flexing hoppers or vibrations create transient demands for compensatory speed adjustments that can only be partially successful.
- The success of Acromet 1000 volumetric feeders, due to the smooth pre-feed product conditioning which providers uniformity of discharge rate, reduces the demands on the control system for compensatory action and thus ensures smoother control with correspondingly improved accuracy.
- Weight differential control
- Continuous loss in weight systems: continuous monitoring and adjustment of the feed rate using closed loop microprocessor control. The general principle used is control of weight differential per unit of time.
- Weigh bath systems: the Acromet feeders discharge into a weigh hopper in a pre-programmed sequence against a given recipe.
- Bath loss in weight systems: the feed mechanism and storage hopper are continuously weighed against a pre-programmed reduction in weight. Feeding ceases upon reaching the predetermined set point. Dual flow rate control is available to optimize accuracy when approaching the set point.
Main Products
metering pumps, dry material feeders, gas chlorinator