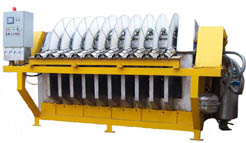
The ceramic filter consists of ceramic filtering plate, rotator, slurry tank, discharge scraper, distributor, agitating device, cleaning device (including ultrasonic cleaning & acid cleaning), frame, vacuum system, pipe system, filtrate discharge system, automatic lubricating system, automatic acid-dosing system, discharge chute, valve and PLC automatic control system (can be made as remote control system).
Driven by the main shaft, the filtering plate rotates to the direction of scraper. Under effect of vacuum system (vacuum pump, filtrate tank, distributor and relevant pipes), the filtering plate below slurry level absorbs the slurry while the filtering plate from slurry level to scraper makes the material (absorbed on it) dry. The filtrate goes into filtrate tank where from it is drained through discharge system (filtrate pump and relevant pipes). When the filtering plate reaches the position of scraper, the cake is taken out by scraper and then given through discharge chute onto conveying belt. After discharge of material, the filtering plate is cleaned in the way of reverse flowing (cleaning takes place once after each circle of rotation). So a few of residue caused by clearance between filtering plate and scraper is cleaned out, and the function of filtering plate is restored during operation.
After certain time (normally, 7 hours), it is necessary to clean the filtering plate by means of detergent (normally, it is nitric acid depending on characteristics of material) and ultrasonic. So the materials & foreign matters stopped in pores of filtering plate or absorbed on surface of filtering plate are cleaned out, and the function of filtering plate is restored during operation.
The ceramic filter adopts PLC full-automatic control system. Both full-automatic operation and manual operation are possible to provide flexibility & convenience.
Driven by the main shaft, the filtering plate rotates to the direction of scraper. Under effect of vacuum system (vacuum pump, filtrate tank, distributor and relevant pipes), the filtering plate below slurry level absorbs the slurry while the filtering plate from slurry level to scraper makes the material (absorbed on it) dry. The filtrate goes into filtrate tank where from it is drained through discharge system (filtrate pump and relevant pipes). When the filtering plate reaches the position of scraper, the cake is taken out by scraper and then given through discharge chute onto conveying belt. After discharge of material, the filtering plate is cleaned in the way of reverse flowing (cleaning takes place once after each circle of rotation). So a few of residue caused by clearance between filtering plate and scraper is cleaned out, and the function of filtering plate is restored during operation.
After certain time (normally, 7 hours), it is necessary to clean the filtering plate by means of detergent (normally, it is nitric acid depending on characteristics of material) and ultrasonic. So the materials & foreign matters stopped in pores of filtering plate or absorbed on surface of filtering plate are cleaned out, and the function of filtering plate is restored during operation.
The ceramic filter adopts PLC full-automatic control system. Both full-automatic operation and manual operation are possible to provide flexibility & convenience.
Features
- Ceramic Filter
- ceramic filter adopts PLC full-automatic control system. Both full-automatic operation and manual operation are possible to provide flexibility & convenience.
Main Products
vacuum ceramic filter