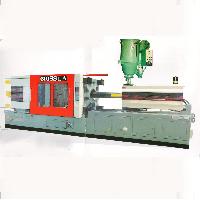
Features
- Multi-Functional LCD display screen
- With memory of 100 molding conditions, 30 points for input and 30 points for output, The setting and modifying of all the data are made by using sheet keys on the control panel, and displayed on the LCD screen, making the operation more conveniently and efficiently performed.
- In addition, bright LCD display with back-light is easy to read under any circumstances.
- Digital LED indication:
- Clearly indicating the temperature, pressure, speed, timing and position of every function simultaneously with each cycle process to procure clear comparison between preset and actual digits of data: counts, temperatures of barrel, and positions.
- New SS2-A series:
- Connect the micro-processor with linear position transducers for clamping and injection units to precisely monitor the position of injection, screw rotate, and mold closing and opening, reducing the breakdown and raising the productivity.
- Lubrication-free design of the toggles and tie-bars. Specially designed oil-free bushings, coated with multi-layers of molybdenum trisulfide membrane, are used in the toggles and tie bars to enable a long-time operation without greasing.
- Hydraulic motor drives the spur gear indirectly and then adjusts the mould thickness. In addition, our own company developed auto-micro adjustment device exclusively, making mould adjustment quicker and more precise.
- All the contact areas of mould platens with fully oil-free dry-type bearings match wear-resistant steel bands for low-friction movements to increase its efficiency and life
- Standard T slot type clamper, matched with screw holes, makes mould checking more convenient and prolongs the life of moulds.
- The moving platen is supported on extra-hard pads which equipped with fully oil-free dry-type bearings and the supported pads slide on ground steel bands. This ensures the mould platen more stable and the machine frame cleaner
- Vertical action double toggle system is in accordance with mechanical requirements. They have wide points of application, multiple magnifying rate and uniform deflection, ensure moulded products maintain their natural characteristics
- Automatic barrel-purging device
- Memory of 100 molding conditions
- Four stages of injection, three stages of holding pressure
- Barrel temperature control by P.I.D process
- Three stages of backpressure functions
- Double-displacement pump
- Highly-responsive logical valves
- Linear position transducers
- Automatic mold-height adjustment
- Detecting the over-shot of injection
Item/Model | unit | 80-SS2A | 100-SS2A | 130-SS2A | 160-SS2A | 200-SS2A | 250-SS2A | 300-SS2A | 400-SS2A | 500-SS2A | 600-SS2A | 700-SS2A | 850-SS2A | 1000-SS2A | 1250-SS2A | 1500-SS2A |
---|---|---|---|---|---|---|---|---|---|---|---|---|---|---|---|---|
Injection unit / screw diameter | mm | 28/32 | 36/40 | 40/45 | 45/50 | 50/55 | 55/60 | 60/65 | 70/75 | 75/80 | 80/85 | 85/90 | 95/100 | 100/105 | 110/120 | 120/135 |
Injection unit / injection pressure | kg/cm square | 1907/1465 | 2021/1637 | 1934/1528 | 1849/1498 | 1900/1570 | 2063/1733 | 1858/1583 | 1617/1408 | 1553/1365 | 1592/1410 | 1612/1438 | 1371/1238 | 1664/1509 | 1444/1213 | 1560/1232 |
Injection unit / theoretical shot volume | cm^3 | 96/126 | 183/226 | 264/334 | 365/451 | 530/641 | 712/848 | 848/995 | 1423/1634 | 1634/1859 | 1859/2099 | 2552/2861 | 3188/3532 | 4082/4500 | 5132/6107 | 6786/8588 |
Injection unit / shot weight of injection (PS) | g | 84/110 | 160/198 | 231/292 | 319/395 | 464/561 | 623/742 | 742/871 | 1246/1430 | 1430/1627 | 1627/1826 | 2233/2504 | 2790/3091 | 3572/3938 | 4491/5344 | 5938/7515 |
Injection unit / injection rate | cm^3/sec | 42/55 | 73/90 | 95/110 | 112/146 | 150/173 | 178/213 | 220/267 | 275/348 | 365/440 | 440/480 | 524/645 | 560/683 | 650/732 | 780/885 | 860/1140 |
Injection unit / plasticizing capacity (PS) | kg/hr | 17/29 | 35/48 | 55/68 | 95/120 | 130/155 | 170/185 | 185/208 | 235/254 | 254/270 | 270/300 | 290/310 | 332/357 | 380/450 | 513/561 | 561/623 |
Mould clamping unit / mould clamping force | tons | 80 | 100 | 130 | 160 | 200 | 250 | 300 | 400 | 500 | 600 | 650 | 850 | 1000 | 1250 | 1500 |
Mould clamping unit / mould opening stroke | mm | 215 | 280 | 320 | 390 | 490 | 540 | 575 | 675 | 745 | 845 | 900 | 1000 | 1100 | 1200 | 1430 |
Mould clamping unit / distance between tie rods | mm | 314 x 238 | 360 x 320 | 410 x 370 | 440 x 400 | 500 x 500 | 550 x 550 | 576 x 576 | 680 x 680 | 750 x 750 | 850 x 850 | 900 x 900 | 980 x 980 | 1050 x 1050 | 1280 x 1280 | 1400 x 1400 |
Mould clamping unit / mould height | mm | 80-320 | 100-370 | 120-450 | 150-480 | 180-550 | 200-580 | 200-620 | 250-700 | 300-780 | 320-850 | 360-920 | 400-1150 | 450-1230 | 500-1450 | 500-1550 |
Mould clamping unit / ejector stroke | mm | 60 | 70 | 90 | 115 | 130 | 145 | 160 | 180 | 220 | 220 | 250 | 250 | 250 | 260 | 280 |
Mould clamping unit / ejector force | tons | 3.5 | 3.5 | 3.5 | 4 | 4 | 4.5 | 4.5 | 8 | 8 | 8 | 14 | 14 | 20 | 20 | 36 |
Electrical equipment / pump driving motor | Hp | 7.5 | 15 | 20 | 25 | 30 | 40 | 40 | 50 | 60 | 60 | 50+30 | 50+50 | 75+50 | 75+75 | 75+75+50 |
Electrical equipment / heater | KW | 4.3 | 5.3 | 5.8 | 6.4 | 8.4 | 10 | 11.7 | 20.5 | 22.5 | 24.3 | 26 | 32 | 38 | 42.8 | 47 |
Electrical equipment / temperature zones | zones | 3 | 4 | 4 | 4 | 5 | 5 | 5 | 7 | 7 | 7 | 8 | 8 | 9 | 9 | 10 |
General / machine weight | kg | 2500 | 3200 | 4200 | 5000 | 7500 | 8600 | 9800 | 18500 | 24500 | 26000 | 29000 | 38000 | 44000 | 52000 | 63000 |
General / machine dimensions | m | 3.8 x 0.8 x 1.6 | 4.6 x 1.2 x 1.65 | 5.1 x 1.3 x 1.7 | 6 x 1.35 x 1.7 | 6.5 x 1.4 x 1.8 | 6.9 x 1.5 x 1.8 | 7.2 x 1.65 x 1.85 | 8.9 x 1.8 x 2.0 | 9.5 x 2.0 x 2.0 | 9.5 x 2.1 x 2.1 | 11.5 x 2.2 x 2.4 | 12.8 x 2.4 x 2.5 | 14 x 2.5 x 2.6 | 15.4 x 2.7 x 2.8 | 16.8 x 3.0 x 3.2 |
Main Products
plastic injection molded machinery