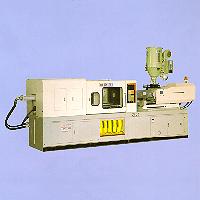
Specifications
- Injection system:
- Twin cylinder injection system made of meehanite cast iron with low resistance.
- Injection cylinder and feed control are set with optical linear ruler with a tolerance of 0.01mm.
- The injection cylinder shot weight can be set to a tolerance and abnormalities can be detected by means of a built in sensors.
- The optional function of withdrawal before and after injection.
- A sliding plate on the hopper is used to ease the unloading and changing of different materials.
- Mold clamping system:
- The mold-locking device incorporates a 5 point double elbow design.
- All moving parts are fitted with special grease packed bushes and not oil feed, to reduce the risk of product contamination. The bushes remain contamination free, are easy to maintain and should be re- greased every 3 months.
- The position of the mold opening and closing is set by means of a linear optical ruler.
- The adjustment of the distance between the fixed and moving halves of the mold is controlled by means of detecting the teeth on the mold carriage with a photo sensor.
- A low pressure system is incorporated into the mold clamping to protect the mold from foreign objects and the operator from danger.
- A sensitive proximity switch is used in conjunction with the injection system. The injection action can be set at different modes i.e. a) Vibration b)Timing c) Ejection under maintained pressure-to suit requirements. This can be used in conjunction with the mold or the option of using the optical ruler.
- Special screw cylinder
- A German premium quality aluminum chrome alloy, which has a nitrognized treated surface to give a very finish that is low friction and corrosion resistant. It therefore has a longer service life than the average screw cylinder.
- The screw the plasticity needed to make it ideal for use with today's engineering plastics.
- Hydraulic system:
- The multistage pump is computer controlled making it very responsive, efficient and precise with a stable output.
- A logical hydraulic pipe arrangement with low noise output and trouble free service. (for machines over 250T)
- It is suggested that the machine is purchased equipped with a bypass type oil filter, insuring reliable operation. (We recommend an Italian external oil filter which is easy to maintain on the large capacity machines)
- Computerized control:
- The control unit is touch operated with a total of 14 different settings, including integral and individual settings for speed and pressure. All settings are digital making control easier and more accurate.
- The display screen for the computer control (APC 5000 specification) is available in different languages is available, these being Chinese, English, French and German.
- Mold information can be stored in a host computer. It is able to store more than 20 groups of data and it can also be connected with an IBM PC (RS 232 online operation memory card can be used for the storage of large amounts of data and printing).
- The system is able to simultaneously display the actual injection pressure curve on the screen. This design will enable a comparison to be made with the required settings and for it to be stored on the memory card, so easy analysis can be made and the quality of production maintained.
Features
- Super speed, high precision, multipurpose, high quality.
- Accuracy:
- Accurate clamping with high rigidity and precision.
- Long opening stroke capacity.
- Top grade materials used.
- Labor saving: Precise automatic locating device to enable easy mold replacement.
- Quiet operation: The hydraulic system uses special low noise pumps for quiet operation.
- Efficient molding: A high compounding screw producing high plasticity.
- Energy saving: Efficient multistage pump for the high capacity machines of more than 250 tons and over.
- High capacity: High output with high efficiency.
- High efficiency: High speed stable injection system.
- High precision: Precision mold locking system.
- High performance safety system highly efficient service network.
- Standard fittings and accessories:
- Hydraulic protection and safety system.
- Standard threaded hydraulic fittings are used.
- Logical hydraulic pipe system.
- Highly sensitive, low pressure mold protection system.
- Differential pipe line for mold closing.
- An automatic photo sensor monitoring system for fine mold adjustment.
- A fitted hand greaser.
- Dryer.
- Compressed air ejection system.
- Oil temperature control system.
- The option of short or long nozzles.
- A set of hand tools with tool box.
- A set of angle brackets and bolts for mold mounting.
- Vibration absorber.
- Grease gun.
- Sumitomo Pump (made in Japan).
- Double-stage pump is fitted to machines over 250T capacity.
- Intermot Calonzi feed unit drive motor (made in Italy).
- Omoro electrical fittings are used.
- Daikin flow direction valves are used.
- Rexroth flow rate unit is used (made in Japan).
- The mold mounting plates and toggle assembly are made of FCD50 material.
- All the injection screws are made from German material.
- Special fittings:
- Optional parallel hydraulic pipe line (capable of a 30% energy saving).
- Load sensitive hydraulic pump (capable of a 50% energy saving).
- Optical ruler for clamping.
- Optical ruler for injecting.
- Linear scale for ejection.
- Computer screen.
Models | SJ-100NT | SJ-120NT | SJ-150NT | SJ-200NT | SJ-250NT | SJ-300NT | SJ-350NT | SJ-500NT | SJ-650NT | SJ-800NT | SJ-1000NT | SJ-1300NT | SJ-1600NT | SJ-2000NT |
---|---|---|---|---|---|---|---|---|---|---|---|---|---|---|
Screw Diameter (dia. mm) | 35/38/42 | 38/42/45 | 40/45/50 | 48/52/55 | 5255/60 | 60/65/70 | 65/70/75 | 75/85/90 | 80/90/100 | 90/100/110 | 100/110/120 | 110/115/130 | 120/130/140 | 130/140/150 |
Shot Size (P.S.) cm^3 | 168/198/242 | 227/278/318 | 276/360/432 | 416/488/546 | 509/570/678 | 820/962/1116 | 1095/1269/1457 | 1767/2269/2544 | 2260/2861/3532 | 3053/3770/4561 | 4084/4942/5581 | 5416/5917/7565 | 7351/8623/10005 | 9291/10770/12370 |
Shot Weight (P.S.) (gr) | 144/169/207 | 194/238/272 | 236/299/369 | 356/417/467 | 435/478/580 | 702/823/955 | 937/1086/1247 | 1512/1942/2177 | 1934/2449/3023 | 2613/3227/3904 | 3495/4230/5034 | 4983/5444/6960 | 6763/7696/9205 | 8547/9612/11380 |
Shot Weight (P.S.) (oz) | 5.0/5.9/7.2 | 6.8/8.3/9.5 | 8.3/10.5/12.9 | 12.5/14.6/16.4 | 15.3/17.1/20.4 | 24.7/28.9/33.6 | 32.9/38.2/43.9 | 53.2/68.3/76.6 | 68/86/106 | 92/113/137 | 123/149/177 | 175/191/245 | 238/271/324 | 300/338/400 |
Plasticizing Capacity (P.S.) (kg/hr) | 46/59/79 | 59/79/98 | 68/68/133 | 81/96/108 | 101/122/160 | 111/141/177 | 145/184/222 | 244/363/424 | 323/479/639 | 421/573/758 | 671/908/1169 | 503/550/703 | 660/775/899 | 606/703/807 |
Injection Pres. (cm^3/sec) | 77/90/110 | 95/116/133 | 121/158/190 | 125/146/164 | 174/195/232 | 224/262/205 | 267/310/356 | 329/422/473 | 442/559/691 | 530/655/793 | 673/815/969 | 959/1048/1339 | 1021/1198/1390 | 1181/1370/1573 |
Injection Pressure (kg/cm^3) | 2057/1745/1428 | 2080/1702/1483 | 2105/1663/1347 | 2050/1747/1562 | 1988/1777/1493 | 1958/1668/1438 | 1988/1714/1493 | 1999/1556/1388 | 2050/1620/1312 | 2074/1680/1388 | 1888/1560/1311 | 1836/1680/1314 | 2042/1740/1500 | 1994/1720/1498 |
Screw Speed (rpm) | 0.220 | 0.210 | 0.180 | 0.137 | 0.149 | 0.150 | 0.162 | 0.156 | 0.185 | 0.152 | 0.151 | 0.161 | 0.160 | 0.150 |
Clamping Force (ton) | 100 | 120 | 150 | 200 | 250 | 300 | 350 | 500 | 650 | 800 | 1000 | 1300 | 1600 | 2000 |
Clamp Stroke (mm) | 315 | 335 | 414 | 420 | 500 | 550 | 630 | 740 | 900 | 1010 | 1138 | 1250 | 1500 | 1700 |
Mold H (mm) | 100-380 | 110-450 | 120-520 | 120-600 | 150-650 | 200-700 | 200-800 | 250-900 | 300-1150 | 350-1250 | 400-1350 | 500-1400 | 550-1500 | 600-1700 |
Platen Size (mm) | 550 x 550 | 605 x 605 | 660 x 660 | 690 x 690 | 775 x 775 | 870 x 870 | 980 x 980 | 1160 x 1160 | 1340 x 1340 | 1440 x 1440 | 1580 x 1580 | 1820 x 1720 | 2100 x 2000 | 2400 x 2250 |
Distance Between Tie-bars (H x V) (mm) | 360 x 360 | 390 x 390 | 430 x 430 | 460 x 460 | 510 x 510 | 560 x 560 | 650 x 650 | 760 x 760 | 860 x 860 | 950 x 950 | 1060 x 1060 | 1220 x 1210 | 1420 x 1320 | 1670 x 1520 |
Ejector Force (ton) | 3.9 | 3.9 | 4.6 | 4.6 | 4.6 | 10.9 | 10.9 | 10.9 | 13.3 | 15.8 | 18.5 | 25 | 25 | 25 |
Ejector Stroke (mm) | 95 | 110 | 125 | 145 | 170 | 180 | 220 | 240 | 260 | 280 | 300 | 320 | 350 | 400 |
Pump Motor (HP) | 15 | 20 | 25 | 30 | 30 | 40 | 50 | 60 | 75 | 100 | 120 | 160 | 200 | 225 |
Heat Zones (set) | 3 | 4 | 4 | 4 | 5 | 5 | 5 | 6 | 6 | 7 | 7 | 7 | 8 | 9 |
Heater Capacity (K W) | 5.6 | 6.2 | 8.1 | 10.2 | 12.5 | 16.5 | 20.5 | 24 | 27.5 | 35 | 42 | 50 | 60 | 70 |
Machine Size (L x W x H) (m) | 4.27 x 1.15 x 1.52 | 4.8 x 1.2 x 1.57 | 5.26 x 1.32 x 1.63 | 6.27 x 1.31 x 1.66 | 6.76 x 1.39 x 1.77 | 7.04 x 1.52 x 1.93 | 7.8 x 1.77 x 1.84 | 8.7 x 1.91 x 1.93 | 10.2 x 2.3 x 2.4 | 10.8 x 2.47 x 2.6 | 12.4 x 2.7 x 2.6 | 12.4 x 2.8 x 2.6 | 15.5 x 3.2 x 3.4 | 17 x 3.5 x 4.0 |
Machine Weight (ton) | 4.3 | 5 | 6.5 | 7.9 | 9.2 | 11.2 | 17.1 | 22.6 | 33 | 45 | 55 | 86 | 95 | 120 |
Machine Weight (gross) (ton) | 4.5 | 5.2 | 6.75 | 8.15 | 9.5 | 11.55 | 17.7 | 23.1 | 36 | 49 | 60 | 92 | 102 | 128 |
Main Products
plastic injection molding machines