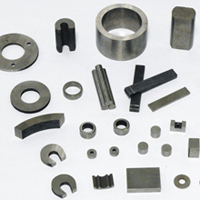
Sintered AlNiCo magnet
AlNiCo material is comprised of aluminum,nickel,cobalt and iron with varying additions of other elements.There are two different manufacturing processes for AlNiCo:Cast and sintered.Cast AlNiCo can be made into many sizes and shapes,whereas Sintered AlNiCo is usually restricted to smaller sizes.However,both processes lead themselves to complex geometries and configurations.Standard Sintered AlNiCo has tighter dimensional tolerances due to its processing.It also has slighty lower magnetic properties,but better mechanical strength than Cast AlNiCo products.They are most suitable for small sizes that are less than 1 oz. It also results in parts that are structurally stronger than the cast alnico magnets. With the sintering process, one can achieve relatively close tolerances without any grinding.
Sintered Alnico magnets are formed by compacting fine Alnico powder in a press and then sintering the compacted powder into a solid magnet. The powdered mixture of contents is pressed into a die under tons of pressure. It is then sintered in a hydrogen atmosphere at 2300F and then cooled – either within a magnetic field or without a magnetic field. When cooled within the magnetic field it is known as an anisotropic magnet and when cooled outside of a magnetic field it is called an isotropic magnet. The sintering process is well suited to large volume production.
Attributes of Alnico Magnets:High mechanical strength, suitable for small volume magnets with complex shape.
Working temperature can reach 550-600 °C
Does not lend itself to conventional machining (hard and brittle)
Good corrosion resistance;
High residual induction and energy product compared to ceramic material
Excellent temperature stability (temp. coefficient of Br is the smallest among all of the other permanent magnets)
Applications of Alnico Magnets:Relays
Controls
Generators
Receivers
Telephones
Bell ringers
Loudspeakers
Cow magnets
Microphones
AlNiCo material is comprised of aluminum,nickel,cobalt and iron with varying additions of other elements.There are two different manufacturing processes for AlNiCo:Cast and sintered.Cast AlNiCo can be made into many sizes and shapes,whereas Sintered AlNiCo is usually restricted to smaller sizes.However,both processes lead themselves to complex geometries and configurations.Standard Sintered AlNiCo has tighter dimensional tolerances due to its processing.It also has slighty lower magnetic properties,but better mechanical strength than Cast AlNiCo products.They are most suitable for small sizes that are less than 1 oz. It also results in parts that are structurally stronger than the cast alnico magnets. With the sintering process, one can achieve relatively close tolerances without any grinding.
Sintered Alnico magnets are formed by compacting fine Alnico powder in a press and then sintering the compacted powder into a solid magnet. The powdered mixture of contents is pressed into a die under tons of pressure. It is then sintered in a hydrogen atmosphere at 2300F and then cooled – either within a magnetic field or without a magnetic field. When cooled within the magnetic field it is known as an anisotropic magnet and when cooled outside of a magnetic field it is called an isotropic magnet. The sintering process is well suited to large volume production.
Attributes of Alnico Magnets:High mechanical strength, suitable for small volume magnets with complex shape.
Working temperature can reach 550-600 °C
Does not lend itself to conventional machining (hard and brittle)
Good corrosion resistance;
High residual induction and energy product compared to ceramic material
Excellent temperature stability (temp. coefficient of Br is the smallest among all of the other permanent magnets)
Applications of Alnico Magnets:Relays
Controls
Generators
Receivers
Telephones
Bell ringers
Loudspeakers
Cow magnets
Microphones
Main Products
Magnet, Rera earth, NdFeB, SmCo,Ferrite,AlNiCo,Pot magnets