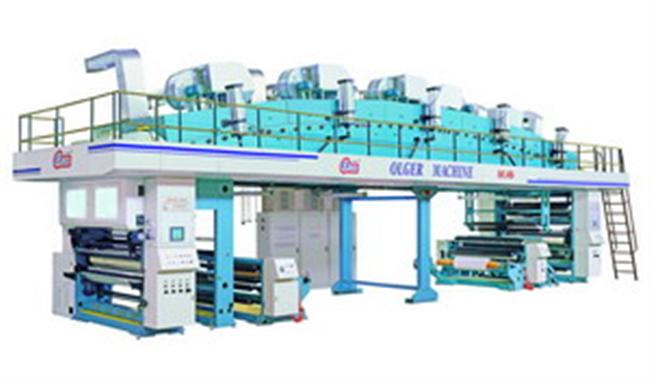
1.Description:This machine is suitable for paper coating processing, such as Laser Transferring Film, Electrified Aluminum Film, Peeling Coating Film and ect.
2.Characteristics:The drying oven adopt Gas Floating Type oven design, its entering/exhausting wind speed is even and superior. The end product drying uniformity and neat degree are good, the chromatic aberration is small. The base film do not run deviation out drying oven. Its dry efficiency is high and the energy consumption is small. This machine is controlled by PLC & operated by an 11” true-color touching monitor and 02 sets of 5.7”HMI (Human-Machine-Interface), achieving the machine parameter’s setting /modifying, monitoring /recording & a work group Production record, producing menu duplication function. it is as a wise choice to improve the product’s consistency and to suit for various production techniques.
3. Main parameter
1) Max coating width: 1600mm
2) Applicants: PET or BOPP film, thickness 12-80um
3) Max winding/unwinding diameter: ф800mm (3”/6” core, air expanding axis)
4) Speed: 80-180m/min.
5) Coating method: Gravure mesh roller transferring method( for option: kiss coating, air
knife or comma scraper)
6) Oven heat source: Oven: 3m x 5sections, electric heating,
60kw/section ( for option: steam, heat-conducting oil, wind oven and so on other heat source) (Far infrared lamp preheating & drying before oven)
7) Power: Driving: about 42kw (excluding oven’s electric heating power)
8) Dimension: 16.45 x 4.1 x 5.058m (L x W x H), height while oven opened: 5.4m
4. Features
4.1. The entire system is integrated controlled by Siemens PLC, with Human-Machine-Interface (HMI) integrated setting, displaying, monitoring & recording for various control points (including speed, tension, temperature control, sucking/exhausting air volume, winding taper parameter, yield & etc.). It can configure multiple production menus to save & repeat production, well for production management.
4.2. Each driving motor adopts ABB inverter motor (with encoder speed-detecting feedback) & vector type inverter controller (closed-loop control with feedback card), achieving more stable running & excellent coating evenness.
4.3. Adopts 4section tension individually setting, integrated setting & displaying in touching monitor, closed-loop control.
4.4. The tension control in oven exist adopts sensitive ultra light floating roller, other tension control adopts Japan Mitsubishi tension sensor, with auto tension compensation and closed-loop control.
4.5. Guide roller for oven driven by individual motor, controlled by inverter (encoder speed-detecting feedback), arc gear synchronizing belt linked move structure, efficiently improved the synchronizing running result of guide roller, can be individually controlled while machine stopped and good to clean.
4.6. Oven temperature control in each section adopts Siemens Temperature Control Module, integrated control by PLC, temperature’s setting & displaying in HMI touching monitor.
4.7. Oven in each section adopts inverter to individually control the air sucking & exhausting, with individual fan to recycle and to work in with the sucking air volume of sucking fan, achieving a optimum technical fan speed & fan pressure, better heat efficiency of oven drying and superior energy saving.
4.8. The oven’s air sucking throttle, recycling throttle and exhausting throttle adopts worm wheel & worm group with flexible shaft coupling. Each air sucking throttle, recycling throttle and exhausting throttle can be adjusting by the oven’s pressure meter on the ground (no need to go up to the oven)
4.9. Fabric winding & unwinding adopts fastener type single channel hydraulic loading & unloading.
4.10. Fabric winding & unwinding adopts central driving, alarm while unwinding roll comes to small, auto speed down to stop while unwinding roll’s diameter comes to set range. Fabric winding can set a preserving roll’s diameter or length, and machine stopped while roll’s diameter comes to set range.
4.11. Winding & unwinding unit adopts Italy Re’s ultrasonic probe EPC system.
2.12. Gantry correcting guide roller with scale meter installed in after unwinding unit, before fabric feeding hauling section, before and after coating head.
4.13. All hauling rubber press roller has pressure spacing device with scale meter.
4.14. Fabric feeding hauling device located before coating head, improve the coating stability.
4.15. Flattening roller& static eraser located before coating.
4.16. Coating head adopts vertical type three roller structure & lift-off fixed length device, with Japan SMC precise pressure adjusting valve (with meter display) at both ends to control pressure, ensuring the fabric not to wrinkle & achieving tighter on/off tension of the coating head’s rubber press roller, increasing end product rate.
4.17. Coating head has auto plate wetting function; the coating roller can be run slowly to wet the plate after machine stopped.
4.18. Scraper adopts individual inverter motor to control swinging at stepless speed adjusting, tri-dimension adjusting & double cylinder pneumatic control.
4.19. Glue supplying device includes glue viscosity automatic tracking control, squirm type pneumatic pump conveying device (recycling work).
4.20. Flattening roller controlled by AC inverter at stepless speed adjusting, clockwise or counter-clockwise turning, speed meter, anti-vibrating device.
4.21. Far infrared lamp located between oven & flattening to pre-heating for drying, good for fabric’s forming & drying at the drying channel.
4.22. Inspecting device with lamp located before winding, to survey the fabric’s coating & drying result.
4.23. Winding tension adopts high sensitive Japan Mitsubishi tension system with closed-loop control, achieving tension’s taper setting & superior winding tension.
4.24. Winding press roller adopts photoelectric sensor tracking & permanent-magnet motor as forward / backward control system & pneumatic control system. A kissing press type or gap type winding tracking system can be chose for excellent winding result.
4.25. Entire machine is integrated controlled by Siemens PLC, running data collecting by an 11inch true-color HMI touching monitor & a 5.7inch HMI touching monitor, achieving parameter’s setting, adjusting, monitoring & recording, single motor individually driving & adjusting, entire machine linked driving & controlling. Lots of emergency stop buttons available around the machine.
4.26. With protection system to prevent speed losing, electricity or voltage overloading, voltage lacking, instant electricity failure, motor overloading or shorten circuit, with idle speed startup protection function.
4.27. Main electrical parts adopt CE or UL qualified products. Electrical box’s protection degree designed as IP21 grade.
2.Characteristics:The drying oven adopt Gas Floating Type oven design, its entering/exhausting wind speed is even and superior. The end product drying uniformity and neat degree are good, the chromatic aberration is small. The base film do not run deviation out drying oven. Its dry efficiency is high and the energy consumption is small. This machine is controlled by PLC & operated by an 11” true-color touching monitor and 02 sets of 5.7”HMI (Human-Machine-Interface), achieving the machine parameter’s setting /modifying, monitoring /recording & a work group Production record, producing menu duplication function. it is as a wise choice to improve the product’s consistency and to suit for various production techniques.
3. Main parameter
1) Max coating width: 1600mm
2) Applicants: PET or BOPP film, thickness 12-80um
3) Max winding/unwinding diameter: ф800mm (3”/6” core, air expanding axis)
4) Speed: 80-180m/min.
5) Coating method: Gravure mesh roller transferring method( for option: kiss coating, air
knife or comma scraper)
6) Oven heat source: Oven: 3m x 5sections, electric heating,
60kw/section ( for option: steam, heat-conducting oil, wind oven and so on other heat source) (Far infrared lamp preheating & drying before oven)
7) Power: Driving: about 42kw (excluding oven’s electric heating power)
8) Dimension: 16.45 x 4.1 x 5.058m (L x W x H), height while oven opened: 5.4m
4. Features
4.1. The entire system is integrated controlled by Siemens PLC, with Human-Machine-Interface (HMI) integrated setting, displaying, monitoring & recording for various control points (including speed, tension, temperature control, sucking/exhausting air volume, winding taper parameter, yield & etc.). It can configure multiple production menus to save & repeat production, well for production management.
4.2. Each driving motor adopts ABB inverter motor (with encoder speed-detecting feedback) & vector type inverter controller (closed-loop control with feedback card), achieving more stable running & excellent coating evenness.
4.3. Adopts 4section tension individually setting, integrated setting & displaying in touching monitor, closed-loop control.
4.4. The tension control in oven exist adopts sensitive ultra light floating roller, other tension control adopts Japan Mitsubishi tension sensor, with auto tension compensation and closed-loop control.
4.5. Guide roller for oven driven by individual motor, controlled by inverter (encoder speed-detecting feedback), arc gear synchronizing belt linked move structure, efficiently improved the synchronizing running result of guide roller, can be individually controlled while machine stopped and good to clean.
4.6. Oven temperature control in each section adopts Siemens Temperature Control Module, integrated control by PLC, temperature’s setting & displaying in HMI touching monitor.
4.7. Oven in each section adopts inverter to individually control the air sucking & exhausting, with individual fan to recycle and to work in with the sucking air volume of sucking fan, achieving a optimum technical fan speed & fan pressure, better heat efficiency of oven drying and superior energy saving.
4.8. The oven’s air sucking throttle, recycling throttle and exhausting throttle adopts worm wheel & worm group with flexible shaft coupling. Each air sucking throttle, recycling throttle and exhausting throttle can be adjusting by the oven’s pressure meter on the ground (no need to go up to the oven)
4.9. Fabric winding & unwinding adopts fastener type single channel hydraulic loading & unloading.
4.10. Fabric winding & unwinding adopts central driving, alarm while unwinding roll comes to small, auto speed down to stop while unwinding roll’s diameter comes to set range. Fabric winding can set a preserving roll’s diameter or length, and machine stopped while roll’s diameter comes to set range.
4.11. Winding & unwinding unit adopts Italy Re’s ultrasonic probe EPC system.
2.12. Gantry correcting guide roller with scale meter installed in after unwinding unit, before fabric feeding hauling section, before and after coating head.
4.13. All hauling rubber press roller has pressure spacing device with scale meter.
4.14. Fabric feeding hauling device located before coating head, improve the coating stability.
4.15. Flattening roller& static eraser located before coating.
4.16. Coating head adopts vertical type three roller structure & lift-off fixed length device, with Japan SMC precise pressure adjusting valve (with meter display) at both ends to control pressure, ensuring the fabric not to wrinkle & achieving tighter on/off tension of the coating head’s rubber press roller, increasing end product rate.
4.17. Coating head has auto plate wetting function; the coating roller can be run slowly to wet the plate after machine stopped.
4.18. Scraper adopts individual inverter motor to control swinging at stepless speed adjusting, tri-dimension adjusting & double cylinder pneumatic control.
4.19. Glue supplying device includes glue viscosity automatic tracking control, squirm type pneumatic pump conveying device (recycling work).
4.20. Flattening roller controlled by AC inverter at stepless speed adjusting, clockwise or counter-clockwise turning, speed meter, anti-vibrating device.
4.21. Far infrared lamp located between oven & flattening to pre-heating for drying, good for fabric’s forming & drying at the drying channel.
4.22. Inspecting device with lamp located before winding, to survey the fabric’s coating & drying result.
4.23. Winding tension adopts high sensitive Japan Mitsubishi tension system with closed-loop control, achieving tension’s taper setting & superior winding tension.
4.24. Winding press roller adopts photoelectric sensor tracking & permanent-magnet motor as forward / backward control system & pneumatic control system. A kissing press type or gap type winding tracking system can be chose for excellent winding result.
4.25. Entire machine is integrated controlled by Siemens PLC, running data collecting by an 11inch true-color HMI touching monitor & a 5.7inch HMI touching monitor, achieving parameter’s setting, adjusting, monitoring & recording, single motor individually driving & adjusting, entire machine linked driving & controlling. Lots of emergency stop buttons available around the machine.
4.26. With protection system to prevent speed losing, electricity or voltage overloading, voltage lacking, instant electricity failure, motor overloading or shorten circuit, with idle speed startup protection function.
4.27. Main electrical parts adopt CE or UL qualified products. Electrical box’s protection degree designed as IP21 grade.
Certificate
- ISO9001:2009 Quality System Certificate and CE approval
Main Products
printing machine,coating machine,printing machine for woven bags