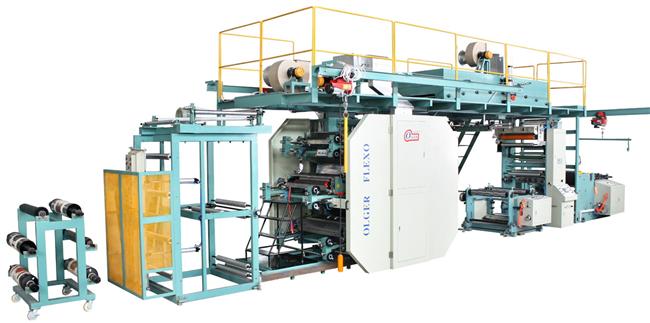
A.Description:
This machine is absorbed some techniques/ technology from Europe in design & manufacture,
with full configuration & all ready function in production. It can do Continuously multi-colors (Front side: 6colors, Back side: 6colors) printing for roll fabric with excellent printing performance, like TUBULAR WOVEN FABRIC/LAMINATED WOVEN FABRIC/PAPER COMBINED WOVEN FABRIC /NON-WOVEN & ect.
B. Characteristic:
1. Printing unit driven by helical gears achieves accurate register & lower noise.
2. Manual quantitative online (in machine running) adjusting device for horizontal & vertical printing registering in printing station, achieving quick online color registering at one time, greatly reduce time consumption to repeatedly pause the machine to adjust printing plate and lose on fabric cost for print testing, mostly improve production efficiency.
3. While machine paused, plate roller/anilox automatic backward released (pneumatic control), avoids printing plate pressed on the fabric in long time; otherwise, this pressed position will be deformed, resulting in inconsistent color printing, and pressing position will also appear ink solidifying and sticking, then the printing plate may be tore when print again.
4. While machine running again, plate roller/anilox is automatically back to position (pneumatic control), ensures the printing pressure and printing accuracy did not be affected by machine stopped or paused operation.
5. Enlarge the diameter of ink roller & anilox to φ127mm, improved their intensity, rigidity & print stability, optimally prevents rollers’ end broken & plate‘s frayed, achieving less dithering, evenly ink offering & printing plate’s durability.
6. Automatic tracking positioning device for front and back side’s pattern positioning.
7. Drying cabinet between printing stations.
8. Twin channel unwinding in machine running status, with automatic EPC system.
9. Chilling roller for fabric forming and hauling in after-printed.
10.Canada Alpha Technology is used on automatical cutting and winding unit; adopt friction –center driven composite winding type and rodless cylinder automatical cutting for changing roll, achieving winding roll in machine running status, to raise productivity and reduce labor intensity.
11. Equipped with three sections auto tension control system in this machine. Tension control is by sensors in winding and unwinding unit. The drying chamber equipped with ultra-light floating roller tension system.
12. Corona treating device adopts TBIG module control, output power can automatically track mechanical speed for self adjusting, ensures the consistency of corona dyne value. Auto power off once machine stopped.
13. Located Static graphics monitoring system in front and back sides(for clients’option & purchases)
C.Main Parameters:
1. Max mechanical speed: 150m/min.
2. Printing speed: 80-140m/min
3. Fabric max width: 800mm
4. Fabric roll max diameter: φ1200mm
5. Max width of winding roll: 800mm
6. Max diameter of winding roll: φ1200mm
7. Printing width: 720mm
8. Change of gear: 10mm(change 1 tooth on the gear corresponding increasing
or decreasing length of 10mm)
9. Printing range : 500-1250mm
10. Printing roller correction: horizontal +/-10mm, vertical+/-10mm,
Online (in machine running) adjustable quantitative device
11. Printing colors: Double sides 12 colors printing
(Front side: 6colors, Back side: 6colors)
12. Printing plate: polymer, 3.94mm thickness (or by client’s option)
13. Plate roller’s printing length: 620mm (or by client’s option)
14. Anilox: φ127 x 720mm (250LPI x 6pcs, 200LPI x 6pcs), Ink rubber roller: φ120 x 815mm
15. Power: 118kw (Motors power: 38kw + Infrared dryers power: 76kw + Corona treator: 4kw)
16. Weight: Approximate 28T
17. Dimension: 19.2 x 4 x 5m (L x W x H)
D. Main components:
1. Twin channel unwinding unit 1unit
2. CI type 06 colors printing unit 2units
3. Drying cabinet between printing stations 10sets
4. Drying chamber in after-printed 1unit
5. Automatic positioning device for front and back side’s pattern positioning
6. Chilly transaction device in after-printed 1set
7. Automatic cutting and winding unit 1unit
8. Automatic double sides corona treating device 1unit
9. Electronic control system
10. Static graphics monitoring system 2sets(for clients’option & purchases)
Remarks: Printing station includes plate roller, anilox, ink rubber roller, printing plate wetting device, ink auto circulation device, online horizontal & vertical color registering device (in machine running status), hydraulic auto positioning device, drying chamber between printing stations and synchronizing control device for printing station.
E. Main Configuration:
Human-Machine-Interface (HMI) & touching monitor: Taiwan HiTech
Contactor, Potentiometer, Button: France SCHNEIDAR
Anode ultra light aluminum guiding roller: Taiwan
Photoelectric correlative sensor: Taiwan YANMING
Auto EPC Taiwan JIN’S
Position proximity switch: Korea
Photoelectric rotating coder: Korea Main pneumatic parts: Taiwan AIRTEC
PLC: SIEMENS Relay: France SCHNEIDAR
Contact breaker: France TE Temperature control: Japan
Main bearing: Japan NSK Inverter motor: Taiwan/China
Limit switch: Taiwan MOUJEN Static brush: Italy
Inverter controller: Japan YASKAWA
This machine is absorbed some techniques/ technology from Europe in design & manufacture,
with full configuration & all ready function in production. It can do Continuously multi-colors (Front side: 6colors, Back side: 6colors) printing for roll fabric with excellent printing performance, like TUBULAR WOVEN FABRIC/LAMINATED WOVEN FABRIC/PAPER COMBINED WOVEN FABRIC /NON-WOVEN & ect.
B. Characteristic:
1. Printing unit driven by helical gears achieves accurate register & lower noise.
2. Manual quantitative online (in machine running) adjusting device for horizontal & vertical printing registering in printing station, achieving quick online color registering at one time, greatly reduce time consumption to repeatedly pause the machine to adjust printing plate and lose on fabric cost for print testing, mostly improve production efficiency.
3. While machine paused, plate roller/anilox automatic backward released (pneumatic control), avoids printing plate pressed on the fabric in long time; otherwise, this pressed position will be deformed, resulting in inconsistent color printing, and pressing position will also appear ink solidifying and sticking, then the printing plate may be tore when print again.
4. While machine running again, plate roller/anilox is automatically back to position (pneumatic control), ensures the printing pressure and printing accuracy did not be affected by machine stopped or paused operation.
5. Enlarge the diameter of ink roller & anilox to φ127mm, improved their intensity, rigidity & print stability, optimally prevents rollers’ end broken & plate‘s frayed, achieving less dithering, evenly ink offering & printing plate’s durability.
6. Automatic tracking positioning device for front and back side’s pattern positioning.
7. Drying cabinet between printing stations.
8. Twin channel unwinding in machine running status, with automatic EPC system.
9. Chilling roller for fabric forming and hauling in after-printed.
10.Canada Alpha Technology is used on automatical cutting and winding unit; adopt friction –center driven composite winding type and rodless cylinder automatical cutting for changing roll, achieving winding roll in machine running status, to raise productivity and reduce labor intensity.
11. Equipped with three sections auto tension control system in this machine. Tension control is by sensors in winding and unwinding unit. The drying chamber equipped with ultra-light floating roller tension system.
12. Corona treating device adopts TBIG module control, output power can automatically track mechanical speed for self adjusting, ensures the consistency of corona dyne value. Auto power off once machine stopped.
13. Located Static graphics monitoring system in front and back sides(for clients’option & purchases)
C.Main Parameters:
1. Max mechanical speed: 150m/min.
2. Printing speed: 80-140m/min
3. Fabric max width: 800mm
4. Fabric roll max diameter: φ1200mm
5. Max width of winding roll: 800mm
6. Max diameter of winding roll: φ1200mm
7. Printing width: 720mm
8. Change of gear: 10mm(change 1 tooth on the gear corresponding increasing
or decreasing length of 10mm)
9. Printing range : 500-1250mm
10. Printing roller correction: horizontal +/-10mm, vertical+/-10mm,
Online (in machine running) adjustable quantitative device
11. Printing colors: Double sides 12 colors printing
(Front side: 6colors, Back side: 6colors)
12. Printing plate: polymer, 3.94mm thickness (or by client’s option)
13. Plate roller’s printing length: 620mm (or by client’s option)
14. Anilox: φ127 x 720mm (250LPI x 6pcs, 200LPI x 6pcs), Ink rubber roller: φ120 x 815mm
15. Power: 118kw (Motors power: 38kw + Infrared dryers power: 76kw + Corona treator: 4kw)
16. Weight: Approximate 28T
17. Dimension: 19.2 x 4 x 5m (L x W x H)
D. Main components:
1. Twin channel unwinding unit 1unit
2. CI type 06 colors printing unit 2units
3. Drying cabinet between printing stations 10sets
4. Drying chamber in after-printed 1unit
5. Automatic positioning device for front and back side’s pattern positioning
6. Chilly transaction device in after-printed 1set
7. Automatic cutting and winding unit 1unit
8. Automatic double sides corona treating device 1unit
9. Electronic control system
10. Static graphics monitoring system 2sets(for clients’option & purchases)
Remarks: Printing station includes plate roller, anilox, ink rubber roller, printing plate wetting device, ink auto circulation device, online horizontal & vertical color registering device (in machine running status), hydraulic auto positioning device, drying chamber between printing stations and synchronizing control device for printing station.
E. Main Configuration:
Human-Machine-Interface (HMI) & touching monitor: Taiwan HiTech
Contactor, Potentiometer, Button: France SCHNEIDAR
Anode ultra light aluminum guiding roller: Taiwan
Photoelectric correlative sensor: Taiwan YANMING
Auto EPC Taiwan JIN’S
Position proximity switch: Korea
Photoelectric rotating coder: Korea Main pneumatic parts: Taiwan AIRTEC
PLC: SIEMENS Relay: France SCHNEIDAR
Contact breaker: France TE Temperature control: Japan
Main bearing: Japan NSK Inverter motor: Taiwan/China
Limit switch: Taiwan MOUJEN Static brush: Italy
Inverter controller: Japan YASKAWA
Certificate
- ISO9001:2008 Quality System Certificate and CE approval
Main Products
printing machine,coating machine,printing machine for woven bags