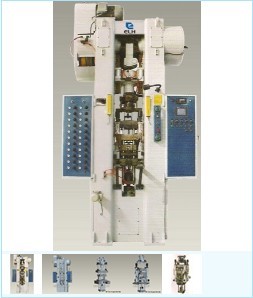
1. USAGE
The powder compacting press is used to process metal powder, precision ceramics, and magnetic material. It is ideal equipment especially when the work piece has many steps and a complicate shape.
2. Performance
a) A high and low limit on the pressure can be set to ensure the density and length of product and the safety of mould and machine.
b) Overfill and less fill mechanism are equipped to correct the molding defects in complicated product and ensure the performance of product
c) The upper punch equips an air pressure reset device to avoid crack on the product when ejecting.
d) The filling in lower 1st and 2nd punch can be adjusted automatically. The shaping height is set by the block, which can also be adjusted. In this way, the product will has correct dimensions and even density in each step.
e) In the seats of the 1st and 2nd lower punch, a powder moving device is equipped. Thus, the condition of density difference can be improved.
f) In the seats of the 1st and 2nd lower punch, an air pressure balancing device is equipped to avoid the punch heads collide with the product and hopper. In this way, a complicated-shaped product can be ejected smoothly and a crack in the product is avoided.
g) The core rod can float automatically so that the ejection force and feeding height for long product with a thin wall can be reduced. Therefore, the utilization ratio of the machine increases.
h) According to the requirements of different products, the die float can be adjusted automatically to ensure the density difference on the upper and lower part of the product.
i) The last pressing device is equipped so that the device can continue to press the product even after the die float stops. In this way, density of the product with steps is more even.
j) CVT (constant variable transmission) on frequency is adopted to regulate the molding speed so that different products’ molding speed requirement can be satisfied.
3. Easy to Operate
a) The machine is driven from the upper position and the transmission loss is small. It needs only a small place to be installed. It is very easy for maintenance and repair.
b) The upper punch body equips an oil pressure tank. If the machine is blocked to stop due to over pressure, just discharge oil in the tank. Then switch on the machine and rotate reversely to eliminate the abnormal. Finally fill oil into the tank and the machine will be in order.
c) All adjustments are controlled by the computer. All the data during adjustment and pressing will be shown on the screen. If any error occurs, the machine will stops automatically.
d) The central electrical lubrication oil pump can lubricate the machine periodically and at a fixed volume. The lubricating system has check and protection functions. In this way, even under bad conditions, the system can be used efficiently.
e) An advanced human-machine interface is adopted. It is very easy to operate.
4. Safety
a) When ejecting, a checking device is equipped to avoid product attaching on an upper punch and rising together with a lower punch. Thus, the mould and the machine can avoid being damaged.
b) It is equipped with examine devices at powder hopper, powder tank, upper stroke, lower stroke, air source pressure, lower 1st and 2nd punch. At the same time, a photoelectrical safety device is installed. All these ensure the safety of machine, mould, product and human body.
The powder compacting press is used to process metal powder, precision ceramics, and magnetic material. It is ideal equipment especially when the work piece has many steps and a complicate shape.
2. Performance
a) A high and low limit on the pressure can be set to ensure the density and length of product and the safety of mould and machine.
b) Overfill and less fill mechanism are equipped to correct the molding defects in complicated product and ensure the performance of product
c) The upper punch equips an air pressure reset device to avoid crack on the product when ejecting.
d) The filling in lower 1st and 2nd punch can be adjusted automatically. The shaping height is set by the block, which can also be adjusted. In this way, the product will has correct dimensions and even density in each step.
e) In the seats of the 1st and 2nd lower punch, a powder moving device is equipped. Thus, the condition of density difference can be improved.
f) In the seats of the 1st and 2nd lower punch, an air pressure balancing device is equipped to avoid the punch heads collide with the product and hopper. In this way, a complicated-shaped product can be ejected smoothly and a crack in the product is avoided.
g) The core rod can float automatically so that the ejection force and feeding height for long product with a thin wall can be reduced. Therefore, the utilization ratio of the machine increases.
h) According to the requirements of different products, the die float can be adjusted automatically to ensure the density difference on the upper and lower part of the product.
i) The last pressing device is equipped so that the device can continue to press the product even after the die float stops. In this way, density of the product with steps is more even.
j) CVT (constant variable transmission) on frequency is adopted to regulate the molding speed so that different products’ molding speed requirement can be satisfied.
3. Easy to Operate
a) The machine is driven from the upper position and the transmission loss is small. It needs only a small place to be installed. It is very easy for maintenance and repair.
b) The upper punch body equips an oil pressure tank. If the machine is blocked to stop due to over pressure, just discharge oil in the tank. Then switch on the machine and rotate reversely to eliminate the abnormal. Finally fill oil into the tank and the machine will be in order.
c) All adjustments are controlled by the computer. All the data during adjustment and pressing will be shown on the screen. If any error occurs, the machine will stops automatically.
d) The central electrical lubrication oil pump can lubricate the machine periodically and at a fixed volume. The lubricating system has check and protection functions. In this way, even under bad conditions, the system can be used efficiently.
e) An advanced human-machine interface is adopted. It is very easy to operate.
4. Safety
a) When ejecting, a checking device is equipped to avoid product attaching on an upper punch and rising together with a lower punch. Thus, the mould and the machine can avoid being damaged.
b) It is equipped with examine devices at powder hopper, powder tank, upper stroke, lower stroke, air source pressure, lower 1st and 2nd punch. At the same time, a photoelectrical safety device is installed. All these ensure the safety of machine, mould, product and human body.
Main Products
25-260 Ton Powder Compacting Press