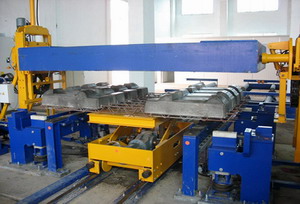
Customisable production solution for concrete sleepers
This production line is designed to fit many needs and requirements, from the reception of aggregates and cement, to the stacking of sleepers before dispatch.
Attentive to the constraints and requirements of its customers, we made its systems customisable and evolutionary, from standard equipment for processes with a low level of automated handling equipment, to the highest level of automation.
The company favours solutions combining ease of use, security, and ergonomics to enable you to achieve the best possible quality and profitable production. Ergonomic workstations are user-optimised, which includes supportive equipment to facilitate rebars handling.
High-capacity railway sleeper production line
Many renowned concrete sleeper producers already trust FIMEC Technologies, appreciating the high capacity, flexibility and reliability of the line. Production rate is about one mould every minute, which means two sleepers (up to 330kg each when mono-block) every minute.
Concrete sleeper production process and equipment
The process is generally undertaken in the following steps:
Aggregate acceptance, storage and batching: truck unloaders, storage towers, hoppers, conveyors and weighting conveyor. Aggregate preparation before mixing with cement
Cement storage and batching: vertical silos and batching by weighing hopper
Mixing and concrete batching: loading of mixer by skip or conveyor, planetary mixer, weighing loaders with fixed or mobile hoppers; extraction by conveyor or screw
Sleeper curing: metal structure, designed to cure concrete naturally or using a heating system, transfer car with built-in shuttle capable of handling up to eight moulds at one time
Mould dehacking: system capable of depositing moulds one at a time on a conveyor ready for subsequent operations.
Stress relief line and heads: the conveyor and the stress relief heads transfer stress to the sleepers
De-moulder: the sleepers are separated from their moulds
Sleeper fitting: the line enables operators to fit accessories to the sleepers and to carry out quality controls
Transfer to the stock: transfer car for completed, stacked sleepers
This production line is designed to fit many needs and requirements, from the reception of aggregates and cement, to the stacking of sleepers before dispatch.
Attentive to the constraints and requirements of its customers, we made its systems customisable and evolutionary, from standard equipment for processes with a low level of automated handling equipment, to the highest level of automation.
The company favours solutions combining ease of use, security, and ergonomics to enable you to achieve the best possible quality and profitable production. Ergonomic workstations are user-optimised, which includes supportive equipment to facilitate rebars handling.
High-capacity railway sleeper production line
Many renowned concrete sleeper producers already trust FIMEC Technologies, appreciating the high capacity, flexibility and reliability of the line. Production rate is about one mould every minute, which means two sleepers (up to 330kg each when mono-block) every minute.
Concrete sleeper production process and equipment
The process is generally undertaken in the following steps:
Aggregate acceptance, storage and batching: truck unloaders, storage towers, hoppers, conveyors and weighting conveyor. Aggregate preparation before mixing with cement
Cement storage and batching: vertical silos and batching by weighing hopper
Mixing and concrete batching: loading of mixer by skip or conveyor, planetary mixer, weighing loaders with fixed or mobile hoppers; extraction by conveyor or screw
Sleeper curing: metal structure, designed to cure concrete naturally or using a heating system, transfer car with built-in shuttle capable of handling up to eight moulds at one time
Mould dehacking: system capable of depositing moulds one at a time on a conveyor ready for subsequent operations.
Stress relief line and heads: the conveyor and the stress relief heads transfer stress to the sleepers
De-moulder: the sleepers are separated from their moulds
Sleeper fitting: the line enables operators to fit accessories to the sleepers and to carry out quality controls
Transfer to the stock: transfer car for completed, stacked sleepers
Main Products
Precast Concrete hollow core slab machine,Hollow core roofslab machine