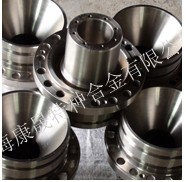
hastelloyC-4
hastelloyC-4 austenitic low-carbon nickel-molybdenum-chromium alloy
Product ID: hastelloyC-4
Send Inquiry
Hastelloy C-4
Features and applications overview:
The alloy is an austenitic low-carbon nickel-molybdenum-chromium alloy. The main difference between Nicrofer 6616 hMo and early developed alloy of similar chemical compositions is the low content of carbon, silicon, iron and tungsten. Such a chemical composition makes excellent stability at 650-1040°C, improves resistance to intergranular corrosion, and under appropriate manufacturing conditions avoids the corrosion of the edge line and of the weld heat affected zone. The alloy is applied in flue gas desulfurization system, pickling and acid regeneration plant, acetic acid and agrochemicals production, titanium dioxide production (chlorine), electrolytic plating, etc.
Hastelloy C-4s similar grade:
NS335(China) W.Nr.2.4610 NiMo16Cr16Ti(Germany)
Chemical composition, %:
Nickel........................................balance
Chromium..................................14.5-17.5
Iron.............................................3.0 max
Molybdenum...............................14.0-17.0
Cobalt.........................................2.0 max
Carbon........................................0.009 max
Manganese..................................1.0 max
Silicon..........................................0.05 max
Sulfur...........................................0.01 max
Phosphorus...................................0.02 max
Titanium..........................................0.7 max
Physical properties:
Density, g/cm3 ..........................8.6
Melting Range, °C................1335-1380
Thermal conductivity, λ/(W/m•°C), at 100°C .......10.1
Specific heat, J/kg•°C....................408
Elastic modulus, GPa.....................211
Electrical resistivity, μΩ•m.............1.24
Coefficient of linear expansion, a/10-6°C-1, at 20-100°C.............10.9
Mechanical properties:(the minimum value detected at room temperature)
Tensile strength, σb/MPa....................690
Yield strength,σp0.2/MPa..............275
Elongation,σ5 /%...................................40
The way of heat treatment is solution treatment
Available products and specifications:
Bar: ASTM B574, ASME SB574
Forging: ASTM B336, ASME SB336
Plate/Strip: ASTM B575, ASME SB575
Pipe: ASTM B622, ASTM B619, ASTM B626, ASME SB622, ASME SB619, ASME626
The metallurgical structure of Hastelloy C-4:
Hastelloy C-4 is of the face-centered cubic lattice structure. Its chemical compositions ensure the stability and the allergy resistance of metallurgical structure.
The process performance and requirements of Hastelloy C-4:
1, The alloy cannot contact sulfur, phosphorus, lead and other low melting point metal during the heat treatment, otherwise the alloy becomes brittle. It should be noted to clear some contaminants such as marking and temperature-indicating paints, crayons, lubricating oil, and fuel. The content of sulfur in fuel should be kept as low as possible. The sulfur content of the gas should be less than 0.1%, and in heavy oil should be less than 0.5%. Electric furnace heating is a better choice, because the electric furnaces precise temperature control and the clean furnace gas. If the furnace gas is pure enough, gas furnace can be an alternate.
2, The thermal processing temperature range of the alloy is 1080°C~900°C. The cooling method is water-cooling or other rapid cooling. To ensure the best performance of anti-corrosion, solution heat treatment should be carried out after the thermal processing.
Features and applications overview:
The alloy is an austenitic low-carbon nickel-molybdenum-chromium alloy. The main difference between Nicrofer 6616 hMo and early developed alloy of similar chemical compositions is the low content of carbon, silicon, iron and tungsten. Such a chemical composition makes excellent stability at 650-1040°C, improves resistance to intergranular corrosion, and under appropriate manufacturing conditions avoids the corrosion of the edge line and of the weld heat affected zone. The alloy is applied in flue gas desulfurization system, pickling and acid regeneration plant, acetic acid and agrochemicals production, titanium dioxide production (chlorine), electrolytic plating, etc.
Hastelloy C-4s similar grade:
NS335(China) W.Nr.2.4610 NiMo16Cr16Ti(Germany)
Chemical composition, %:
Nickel........................................balance
Chromium..................................14.5-17.5
Iron.............................................3.0 max
Molybdenum...............................14.0-17.0
Cobalt.........................................2.0 max
Carbon........................................0.009 max
Manganese..................................1.0 max
Silicon..........................................0.05 max
Sulfur...........................................0.01 max
Phosphorus...................................0.02 max
Titanium..........................................0.7 max
Physical properties:
Density, g/cm3 ..........................8.6
Melting Range, °C................1335-1380
Thermal conductivity, λ/(W/m•°C), at 100°C .......10.1
Specific heat, J/kg•°C....................408
Elastic modulus, GPa.....................211
Electrical resistivity, μΩ•m.............1.24
Coefficient of linear expansion, a/10-6°C-1, at 20-100°C.............10.9
Mechanical properties:(the minimum value detected at room temperature)
Tensile strength, σb/MPa....................690
Yield strength,σp0.2/MPa..............275
Elongation,σ5 /%...................................40
The way of heat treatment is solution treatment
Available products and specifications:
Bar: ASTM B574, ASME SB574
Forging: ASTM B336, ASME SB336
Plate/Strip: ASTM B575, ASME SB575
Pipe: ASTM B622, ASTM B619, ASTM B626, ASME SB622, ASME SB619, ASME626
The metallurgical structure of Hastelloy C-4:
Hastelloy C-4 is of the face-centered cubic lattice structure. Its chemical compositions ensure the stability and the allergy resistance of metallurgical structure.
The process performance and requirements of Hastelloy C-4:
1, The alloy cannot contact sulfur, phosphorus, lead and other low melting point metal during the heat treatment, otherwise the alloy becomes brittle. It should be noted to clear some contaminants such as marking and temperature-indicating paints, crayons, lubricating oil, and fuel. The content of sulfur in fuel should be kept as low as possible. The sulfur content of the gas should be less than 0.1%, and in heavy oil should be less than 0.5%. Electric furnace heating is a better choice, because the electric furnaces precise temperature control and the clean furnace gas. If the furnace gas is pure enough, gas furnace can be an alternate.
2, The thermal processing temperature range of the alloy is 1080°C~900°C. The cooling method is water-cooling or other rapid cooling. To ensure the best performance of anti-corrosion, solution heat treatment should be carried out after the thermal processing.
Certificate
- ISO
Main Products
high temperature alloys, corrosion resistant alloys, precision alloys