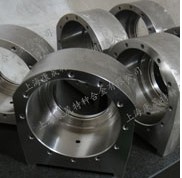
hastelloyX
Hastelloy X nickel-based superalloy
Features and applications overview:
Hastelloy X is a nickel-based superalloy of higher amount of iron. The alloy uses chromium and molybdenum to conduct solid solution strengthening. It has good resistance to oxidation and corrosion. It has medium and lasting creep strength below 900°C. It has good formability and weldability in cold and hot processing. This alloy is suitable for the manufacture of aero-engine combustion chamber components and other high temperature components. It has a long-term usage under 900°C. Short-time working temperature reaches 1080°C.
Hastelloy Xs similar grades:
GH3536 GH536(China)、 NC22FeD(France)、NiCr22FeMo(Germany)、Nimonic PE13(England)
Chemical composition, %
Nickel…………………………balance
Chromium……………………20.5-23.0
Iron……………………………17.0-20.0
Tungsten………………………0.2-1.0
Molybdenum…………………8.0-10.0
Cobalt…………………………0.5-2.5
Carbon…………………………0.05-0.15
Manganese……………………1.0 max
Silicon…………………………1.0 max
Sulfur…………………………0.015 max
Phosphorus……………………0.025 max
Copper…………………………0.5 max
Aluminium……………………0.15 max
Titanium………………………0.5 max
Physical properties:
Density, g/cm3………………………8.28
Melting Range, °C…………………1295-1381
Thermal conductivity, λ/(W/m•°C), at 100°C……13.38
Specific heat, J/kg•°C………………372.6
Elastic modulus, GPa………………199
Electrical resistivity, μΩ•m…………1.18
Coefficient of linear
expansion, a/10-6°C-1, at 20-100°C………12.1
Mechanical properties: (the minimum value detected at room temperature)
Tensile strength, σb/MPa………….690
Yield strength,σp0.2/MPa………275
Elongation,σ5 /%……………………30
Brinell hardness, HBS…………………≥241
The way of heat treatment is solution treatment
Available products and specifications:
Bar: ASTM B572, AMS 5754, ASME SB572
Forging: AMS 5754
Plate/Strip: ASTM B435, AMS 5536, ASME SB 435
Wire: AMS 5798
Pipe: ASTM B622, ASTM B619, ASTM B626, AMS 5587, ASME SB622, ASME SB619, ASME SB626
The metallurgical structure of Hastelloy X :
The organization of the alloy in the solid solution is austenitic matrix, as well as a small amount of TiN and M6C type carbides.
The process performance and requirements of Hastelloy X:
1, The alloy has good cold and hot workability. The forging heat temperature is 1170°C.
2, The average size of the grain size of the alloy is closely related to the forging deformation degree and the final forging temperature.
3, The alloy has a satisfactory weldability. So for welding , argon arc welding, seam welding, spot welding and so on methods are all available.
4, The alloy may be added directly to the furnace whose operating temperature has been heated to the maximum point. Released immediately after the necessary time in insulation, the alloy should be processed to the specifications. If the metal temperature falls below the lowest processing temperature, the metal should be heated again.
3, The adhesion of the surface oxides of the alloy and the welding slags around the weld is stronger than that of stainless steel. It is recommended to use fine grain abrasive belt and fine grain grinding wheel for polishing.
Features and applications overview:
Hastelloy X is a nickel-based superalloy of higher amount of iron. The alloy uses chromium and molybdenum to conduct solid solution strengthening. It has good resistance to oxidation and corrosion. It has medium and lasting creep strength below 900°C. It has good formability and weldability in cold and hot processing. This alloy is suitable for the manufacture of aero-engine combustion chamber components and other high temperature components. It has a long-term usage under 900°C. Short-time working temperature reaches 1080°C.
Hastelloy Xs similar grades:
GH3536 GH536(China)、 NC22FeD(France)、NiCr22FeMo(Germany)、Nimonic PE13(England)
Chemical composition, %
Nickel…………………………balance
Chromium……………………20.5-23.0
Iron……………………………17.0-20.0
Tungsten………………………0.2-1.0
Molybdenum…………………8.0-10.0
Cobalt…………………………0.5-2.5
Carbon…………………………0.05-0.15
Manganese……………………1.0 max
Silicon…………………………1.0 max
Sulfur…………………………0.015 max
Phosphorus……………………0.025 max
Copper…………………………0.5 max
Aluminium……………………0.15 max
Titanium………………………0.5 max
Physical properties:
Density, g/cm3………………………8.28
Melting Range, °C…………………1295-1381
Thermal conductivity, λ/(W/m•°C), at 100°C……13.38
Specific heat, J/kg•°C………………372.6
Elastic modulus, GPa………………199
Electrical resistivity, μΩ•m…………1.18
Coefficient of linear
expansion, a/10-6°C-1, at 20-100°C………12.1
Mechanical properties: (the minimum value detected at room temperature)
Tensile strength, σb/MPa………….690
Yield strength,σp0.2/MPa………275
Elongation,σ5 /%……………………30
Brinell hardness, HBS…………………≥241
The way of heat treatment is solution treatment
Available products and specifications:
Bar: ASTM B572, AMS 5754, ASME SB572
Forging: AMS 5754
Plate/Strip: ASTM B435, AMS 5536, ASME SB 435
Wire: AMS 5798
Pipe: ASTM B622, ASTM B619, ASTM B626, AMS 5587, ASME SB622, ASME SB619, ASME SB626
The metallurgical structure of Hastelloy X :
The organization of the alloy in the solid solution is austenitic matrix, as well as a small amount of TiN and M6C type carbides.
The process performance and requirements of Hastelloy X:
1, The alloy has good cold and hot workability. The forging heat temperature is 1170°C.
2, The average size of the grain size of the alloy is closely related to the forging deformation degree and the final forging temperature.
3, The alloy has a satisfactory weldability. So for welding , argon arc welding, seam welding, spot welding and so on methods are all available.
4, The alloy may be added directly to the furnace whose operating temperature has been heated to the maximum point. Released immediately after the necessary time in insulation, the alloy should be processed to the specifications. If the metal temperature falls below the lowest processing temperature, the metal should be heated again.
3, The adhesion of the surface oxides of the alloy and the welding slags around the weld is stronger than that of stainless steel. It is recommended to use fine grain abrasive belt and fine grain grinding wheel for polishing.
Certificate
- ISO
Main Products
high temperature alloys, corrosion resistant alloys, precision alloys