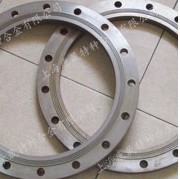
Inconel600
Inconel600 nickel-chromium-iron-based solid solution strengthening alloy
Product ID: Inconel600
Send Inquiry
Inconel600 nickel-chromium-iron-based solid solution strengthening alloy
Features and applications overview:
The alloy is solid solution strengthening of nickel-chromium-iron-based alloy that has good high temperature corrosion and oxidation resistance, excellent hot and cold processing and welding performance, satisfactory thermal strength and high ductility below 700°C. The alloy can be strengthened by cold working, welded by resistance welding, dissolve welding and soldering welding. It is suitable to manufacture antioxidant parts that can bear low load under 1100°C.
Inconel600s similar grades:
GH600 (China) NC15FE(France)、W.Nr.2.4816 NiCr15Fe(Germany) NA14(England)
chemical composition, %:
Nickel + Cobalt.......................72 min
Chromium..................................14.0-17.0
Iron.............................................6.0-10.0
Niobium + Tantalum...................1.0 max
Carbon........................................0.15 max
Manganese..................................1.0 max
Silicon..........................................0.5 max
Sulfur...........................................0.015 max
Phosphorus...................................0.04 max
Copper..........................................0.5 max
Aluminium....................................0.35 max
Titanium........................................0.50 max
Physical properties:
Density, g/cm3 ...........................8.43
Melting Range, °C......................1370-1430
Thermal conductivity,
λ/(W/m•°C), at 100°C ..................12.85
Specific heat, J/kg•°C.....................435
Elastic modulus, GPa.....................205
Shear modulus, GPa.......................76
Electrical resistivity, μΩ•m.............1.05
Poissons ratio.................................0.34
Coefficient of linear expansion,
a/10-6°C-1, at 20-100°C.............12.35
Mechanical properties: (the minimum value detected at room temperature)
Tensile strength, σb/MPa............585
Yield strength,σp0.2/MPa......240
Elongation,σ5 /%..........................30
Brinell hardness, HBS.......................≥217
The way of heat treatment is solution treatment
Available products and specifications:
Bar: ASTM B166, AMS 5665, ASME SB166
Forging: ASTM B166, AMS 5665, ASME SB166
Plate/Strip: ASTM B168, AMS 5540, ASME SB168
Wire: ASTM B166, AMS 5687, ASME SB166
Pipe: ASTM B167, ASTM B163, ASTM B516, ASTM B517, AMS 5580, ASME SB167, ASME SB163, ASME SB163, ASME SB516, ASME SB517
The metallurgical structure of Inconel600:
After two hours of hot-working at 20°C, there are only nitride TiN and cabide Cr7C3 in the structure. After a long-time of 1500 hours processing at 870°C, Cr7C3 and TiN still remain in the structure, which proves the structure of the alloy is stable.
The process performance and requirements of Inconel600:
1, The alloy has good workability. Heating temperature of ingot forging is 1110-1140°C.
2, The average size of the grain size of the alloy is closely related to the forging deformation degree and the final forging temperature.
3, The alloy has good weldability. For welding, methods can be the original electric arc welding, argon arc welding, resistance welding, brazing and so on. Large and complex welded structural components should subject to one hour of annealing at 870°C after fusion welding in order to eliminate welding stress.
4, The alloy shall be machined after heat treatment. Due to the work-hardening of the material, it is appropriate to use lower cutting speed than that of low alloy standard austenitic stainless steel and heavy feed to process, so that the cold hardening alloy can be cut into beneath the surface.
Features and applications overview:
The alloy is solid solution strengthening of nickel-chromium-iron-based alloy that has good high temperature corrosion and oxidation resistance, excellent hot and cold processing and welding performance, satisfactory thermal strength and high ductility below 700°C. The alloy can be strengthened by cold working, welded by resistance welding, dissolve welding and soldering welding. It is suitable to manufacture antioxidant parts that can bear low load under 1100°C.
Inconel600s similar grades:
GH600 (China) NC15FE(France)、W.Nr.2.4816 NiCr15Fe(Germany) NA14(England)
chemical composition, %:
Nickel + Cobalt.......................72 min
Chromium..................................14.0-17.0
Iron.............................................6.0-10.0
Niobium + Tantalum...................1.0 max
Carbon........................................0.15 max
Manganese..................................1.0 max
Silicon..........................................0.5 max
Sulfur...........................................0.015 max
Phosphorus...................................0.04 max
Copper..........................................0.5 max
Aluminium....................................0.35 max
Titanium........................................0.50 max
Physical properties:
Density, g/cm3 ...........................8.43
Melting Range, °C......................1370-1430
Thermal conductivity,
λ/(W/m•°C), at 100°C ..................12.85
Specific heat, J/kg•°C.....................435
Elastic modulus, GPa.....................205
Shear modulus, GPa.......................76
Electrical resistivity, μΩ•m.............1.05
Poissons ratio.................................0.34
Coefficient of linear expansion,
a/10-6°C-1, at 20-100°C.............12.35
Mechanical properties: (the minimum value detected at room temperature)
Tensile strength, σb/MPa............585
Yield strength,σp0.2/MPa......240
Elongation,σ5 /%..........................30
Brinell hardness, HBS.......................≥217
The way of heat treatment is solution treatment
Available products and specifications:
Bar: ASTM B166, AMS 5665, ASME SB166
Forging: ASTM B166, AMS 5665, ASME SB166
Plate/Strip: ASTM B168, AMS 5540, ASME SB168
Wire: ASTM B166, AMS 5687, ASME SB166
Pipe: ASTM B167, ASTM B163, ASTM B516, ASTM B517, AMS 5580, ASME SB167, ASME SB163, ASME SB163, ASME SB516, ASME SB517
The metallurgical structure of Inconel600:
After two hours of hot-working at 20°C, there are only nitride TiN and cabide Cr7C3 in the structure. After a long-time of 1500 hours processing at 870°C, Cr7C3 and TiN still remain in the structure, which proves the structure of the alloy is stable.
The process performance and requirements of Inconel600:
1, The alloy has good workability. Heating temperature of ingot forging is 1110-1140°C.
2, The average size of the grain size of the alloy is closely related to the forging deformation degree and the final forging temperature.
3, The alloy has good weldability. For welding, methods can be the original electric arc welding, argon arc welding, resistance welding, brazing and so on. Large and complex welded structural components should subject to one hour of annealing at 870°C after fusion welding in order to eliminate welding stress.
4, The alloy shall be machined after heat treatment. Due to the work-hardening of the material, it is appropriate to use lower cutting speed than that of low alloy standard austenitic stainless steel and heavy feed to process, so that the cold hardening alloy can be cut into beneath the surface.
Certificate
- ISO
Main Products
high temperature alloys, corrosion resistant alloys, precision alloys