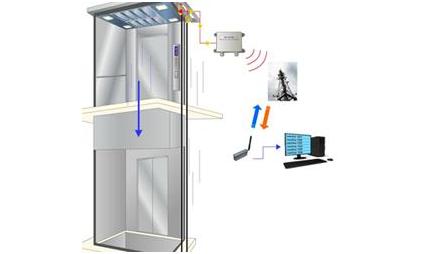
In most cases, elevator breakdowns are the result of users’ feedback. From detection to feedback and acknowledgement of the matter, there is already a time lag, resulting in anxiety and inconvenience. At times, even users’ feedback may be inaccurate. When the matter is finally resolved after on site inspection, testing and remedial work, time and labour cost have been incurred.
The Model WT-1011RC avoids such inconveniences and unnecessary delays. With the Model WT-1011RC supported by a sophisticated software detection system, it will monitor the performance of elevator systems like clockwork with efficiency. With the system in place, it is able to monitor the performance of 500 elevators simultaneously.
The monitoring centre is alerted of any operational anomaly and/or failure before the
end user is aware of the occurrence.
The detection and alert is reported and shown on monitoring screens on computers and via mobile message alerts. The cause of anomaly and/or failure is diagnosed upon detection and confirmation of fault. The system performs a self diagnosis to determine the extent of the fault before feedback is provided to its monitoring base.
Once the extent of fault or failure is confirmed, the monitoring centre personnel in charge has the authority to initiate corrective action such as resetting of the ELCB by turning off and turning on the main power or shut down the elevator system for safety purposes. All these from a remote location via computer interface or via a mobile device as and when deemed fit according to circumstances. A specialist team is despatched on site only when remote access remedial action have not been able to resolve the matter satisfactorily.
Of worthy note is the step by step self-diagnosis ability in the software that eliminates cases of where false alarms are given as a result of pranks and misuse. These often result in specialist teams being sent over at considerable cost only to realise that a false alarm was transmitted because someone decided to play a prank or from deliberate misuse.
For routine performance monitoring, the system is able to chart the total number of times a particular elevator unit ascends or descends its shaft in order to chart an ideal capacity load and optimise its performance based on routine patterns of usage.
Ultimately, the remote monitoring system allows for maximisation of up time, minimising down time while allocating time slots for scheduled maintenance work through an intelligent self diagnosis and appropriate first level responses to genuine faults via remote locations.
It can monitor up to 2 digital inputs. A pre-programmed alarm message can be sent to the pre-programmed phone number when lift failure. The user can also interrogate the inputs through SMS messaging.
It can also be used to monitor the daily operation of lift by counting how many times the lift goes up or down. It is prepared to count pulses of DC=70 ms and T=1.16.
The WT-1011RC also has 2 heavy-duty relay outputs which can be used to reset the lift or set off an audible alarm when lift failure. Output Relay 1 can be permanently switched ON or OFF by calling its phone number, there is no call charges incurred when dialing the unit as it will recognize an authorized telephone number calling it and reject the call without answering. Output Relay 2 can be programmed to switch on for a pre-determined length of time by sending the
Features:
• Support Dual-Band or Quad-Band GSM network
• 2 digital inputs and 2 relay outputs
• Programming can be done by PC (software) or SMS (remotely)
• Monitoring by SMS mobile phone or Software
• Alert notification via SMS (up to 8 telephone numbers)
• Send pre-programmed SMS when lift failure
• Able to monitor up to 500 units with software monitoring
• Reset lift (Output Relay 1) can be done by phone call (No call charges incurred)
• Digital alarm inputs can be used to count pulses (Monitor lift daily operation) or activates the output relay (Set off an audible alarm)
• Backup Lithium rechargeable battery
The Model WT-1011RC avoids such inconveniences and unnecessary delays. With the Model WT-1011RC supported by a sophisticated software detection system, it will monitor the performance of elevator systems like clockwork with efficiency. With the system in place, it is able to monitor the performance of 500 elevators simultaneously.
The monitoring centre is alerted of any operational anomaly and/or failure before the
end user is aware of the occurrence.
The detection and alert is reported and shown on monitoring screens on computers and via mobile message alerts. The cause of anomaly and/or failure is diagnosed upon detection and confirmation of fault. The system performs a self diagnosis to determine the extent of the fault before feedback is provided to its monitoring base.
Once the extent of fault or failure is confirmed, the monitoring centre personnel in charge has the authority to initiate corrective action such as resetting of the ELCB by turning off and turning on the main power or shut down the elevator system for safety purposes. All these from a remote location via computer interface or via a mobile device as and when deemed fit according to circumstances. A specialist team is despatched on site only when remote access remedial action have not been able to resolve the matter satisfactorily.
Of worthy note is the step by step self-diagnosis ability in the software that eliminates cases of where false alarms are given as a result of pranks and misuse. These often result in specialist teams being sent over at considerable cost only to realise that a false alarm was transmitted because someone decided to play a prank or from deliberate misuse.
For routine performance monitoring, the system is able to chart the total number of times a particular elevator unit ascends or descends its shaft in order to chart an ideal capacity load and optimise its performance based on routine patterns of usage.
Ultimately, the remote monitoring system allows for maximisation of up time, minimising down time while allocating time slots for scheduled maintenance work through an intelligent self diagnosis and appropriate first level responses to genuine faults via remote locations.
It can monitor up to 2 digital inputs. A pre-programmed alarm message can be sent to the pre-programmed phone number when lift failure. The user can also interrogate the inputs through SMS messaging.
It can also be used to monitor the daily operation of lift by counting how many times the lift goes up or down. It is prepared to count pulses of DC=70 ms and T=1.16.
The WT-1011RC also has 2 heavy-duty relay outputs which can be used to reset the lift or set off an audible alarm when lift failure. Output Relay 1 can be permanently switched ON or OFF by calling its phone number, there is no call charges incurred when dialing the unit as it will recognize an authorized telephone number calling it and reject the call without answering. Output Relay 2 can be programmed to switch on for a pre-determined length of time by sending the
Features:
• Support Dual-Band or Quad-Band GSM network
• 2 digital inputs and 2 relay outputs
• Programming can be done by PC (software) or SMS (remotely)
• Monitoring by SMS mobile phone or Software
• Alert notification via SMS (up to 8 telephone numbers)
• Send pre-programmed SMS when lift failure
• Able to monitor up to 500 units with software monitoring
• Reset lift (Output Relay 1) can be done by phone call (No call charges incurred)
• Digital alarm inputs can be used to count pulses (Monitor lift daily operation) or activates the output relay (Set off an audible alarm)
• Backup Lithium rechargeable battery
Main Products
WT 9001,WT 9002,WT 9003 and so on
Contact Detail
-
Sales Contact6016-4576042