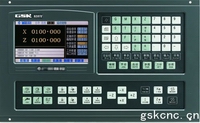
GSK980TDb
GSK980TDb
GSK980TDb is a new product based on GSK980TDa, and its software and hardware are upgraded, which controls 5 feeding axes (including C axis), 2 analog
spindles, 2ms interpolation in high speed, 0.1 um control precision, which obviously improve the efficiency, precision and surface quality of parts
processing. New USB interface, it supports the file operation and program running in flash disk. As the upgraded product of GSK980TDa, GSK980TDb is the best
choice of CNC lathe for the technical upgrading in economical type.
1-Five axes of X, Z, Y, 4th and 5th control, the axial name and type of Y, 4th and 5th can be defined.
2-2ms interpolation cycle, precision of 1um or 0.1um can be selected.
3-Maximum speed 60m/min (When it is 0.1um, the maximum speed is 24m/min).
4-Adapted servo spindle can realize spindle continuous position, rigid tapping, rigid screw processing
5-Built-in many PLC programs, the current running PLC program can be selected
6-G71 command supports the cycle cutting of groove shape outline
7-Support the programming of macro command in sentence type and the calling of macro program with parameter.
8-Support programming in metric system/inch system, with function of auto tool-setting, auto chamfering, tool life management.
9-Display in Chinese, English, Spanish or Russian, which is selected by parameter.
10-With USB interface, it supports file operation in flash disk, system configuration and software upgrade.
11-Analog voltage output of 0V~10V in two channels, support double spindles
12-Electrical MPG input in one channel, it supports hand electrical MPG.
13-Common input in 40 points/common output in 32 points
14-Overall installation dimension and the command system are completely compatible with GSK980TDa.
15-Number of control axes
16-Number of control axes: five axes (X, Z, Y, 4th and 5th )
17-Number of linkage axes: three axes
18-Number of PLC control axes: four axes
19-Feeding axes function
20-Minimum command unit: 0.001mm or 0.0001mm is selectable
21-Position command range: ±99999999 × minimum command unit
22-24m/min Rapid traverse speed: When the command unit is 0.001mm, the maximum speed is 60m/min. 0.0001mm, the maximum speed is 24m/min.
23-Rapid override: Total four levels: F0, 25%, 50% and 100%, real-time adjusting
24-Feeding override: Total 16 levels: 0~150%, real-time adjusting
25-Interpolation mode: Interpolation of linear, arc (support arc interpolation of three points), thread, ellipse and parabola and rigid tapping.
26-Auto chamfering
27-Thread
28-Common thread (follow the spindle)/rigid thread
29-Single-headed/multiple thread of straight, taper and terminal surface in metric system/inch system, equal and variable pitch thread
30-Thread retraction length, angle and speed characteristics can be set
31-Thread pitch: 0.01mm~500mm or 0.06 tooth/inch~25,400 tooth/inch
32-Acceleration and deceleration function
33-Cutting feeding: Linear type or index type is selectable.
34-Rapid traverse: Linear type or S typeThread cutting: Linear type or index type is selectable.
35-The starting speed, finishing speed and time of acceleration and deceleration are set by the parameter.
36-Spindle function
37-Analog voltage 0V~10V output in two channels, support two-spindle control.
38-Spindle encoder feedback in one channel, the resolution of spindle encoder can be set(100p/r~5000p/r).
39-The transmission ratio between encoder and spindle is: (1~255): (1~255)
40-Spindle speed: It is set by S code or PLC signal, the speed range is 0rpm~9999rpm.
41-Spindle override: Total 8 levels: 50%~120%, real-time adjusting
42-Spindle constant surface speed control
43-Rigid tapping
44-Tool function
45-Tool length compensation
46-Tool nose radius compensation (C type)
47-Tool wearing compensation
48-Tool life management
49-Method of setting tools: Tool-setting in fixed position, trial cutting tool-setting, return to reference point, auto tool-setting
50-Tool offset executing mode: Rewriting coordinate mode, tool traverse mode
51-Precision compensation
52-Backlash compensation
53-Pitch error compensation in memory type
54-PLC function
55-PLC program in two levels, maximum 5,000 steps, the refresh cycle of the 1st level program: 8ms
56-PLC program communication download
57-Support PLC warning and PLC alarm
58-Support many PLC programs (maximum 16), the current running PLC program can be selected
59-Basic I/O: input in 40 points/output in 32 points
60-Man-machine interface
61-7.4″large screen LCD, the resolution is 234×480
62-Display in Chinese, English, Spanish or Russian, etc
63-Display in two-dimensional tool path
64-Real-time clock
65-Operation management
66-Operation mode: Edit, auto, MDI, mechanical zero return, MPG/single step, manual, program zero-return
67-Operation authority of multiple-level management
68-Alarm record
69-Editing program
70-Program capacity: 25M, 10,000 programs (including subprograms, macro programs)
71-Editing function: program/block/characters research, rewriting and deleting
72-Program format: ISO code, support macro command programming in sentence type, programming of relative coordinate, absolute coordinate and hybrid
coordinate.
73-Calling program: Support macro program with parameter, subprogram nesting of 4 layers.
74-Community function
75-RS232: Files of part program and parameter, etc can be transmitted in two-way, support PLC program, serial ports of software upgrade.
76-USB: File operation and file directly processing in flash disk, support PLC programs, flash disk of software upgrade.
77-Safety function
78-Emergency stop
79-Hardware travel limit
80-Software travel limit
81-Data restoring and recovering
GSK980TDb is a new product based on GSK980TDa, and its software and hardware are upgraded, which controls 5 feeding axes (including C axis), 2 analog
spindles, 2ms interpolation in high speed, 0.1 um control precision, which obviously improve the efficiency, precision and surface quality of parts
processing. New USB interface, it supports the file operation and program running in flash disk. As the upgraded product of GSK980TDa, GSK980TDb is the best
choice of CNC lathe for the technical upgrading in economical type.
1-Five axes of X, Z, Y, 4th and 5th control, the axial name and type of Y, 4th and 5th can be defined.
2-2ms interpolation cycle, precision of 1um or 0.1um can be selected.
3-Maximum speed 60m/min (When it is 0.1um, the maximum speed is 24m/min).
4-Adapted servo spindle can realize spindle continuous position, rigid tapping, rigid screw processing
5-Built-in many PLC programs, the current running PLC program can be selected
6-G71 command supports the cycle cutting of groove shape outline
7-Support the programming of macro command in sentence type and the calling of macro program with parameter.
8-Support programming in metric system/inch system, with function of auto tool-setting, auto chamfering, tool life management.
9-Display in Chinese, English, Spanish or Russian, which is selected by parameter.
10-With USB interface, it supports file operation in flash disk, system configuration and software upgrade.
11-Analog voltage output of 0V~10V in two channels, support double spindles
12-Electrical MPG input in one channel, it supports hand electrical MPG.
13-Common input in 40 points/common output in 32 points
14-Overall installation dimension and the command system are completely compatible with GSK980TDa.
15-Number of control axes
16-Number of control axes: five axes (X, Z, Y, 4th and 5th )
17-Number of linkage axes: three axes
18-Number of PLC control axes: four axes
19-Feeding axes function
20-Minimum command unit: 0.001mm or 0.0001mm is selectable
21-Position command range: ±99999999 × minimum command unit
22-24m/min Rapid traverse speed: When the command unit is 0.001mm, the maximum speed is 60m/min. 0.0001mm, the maximum speed is 24m/min.
23-Rapid override: Total four levels: F0, 25%, 50% and 100%, real-time adjusting
24-Feeding override: Total 16 levels: 0~150%, real-time adjusting
25-Interpolation mode: Interpolation of linear, arc (support arc interpolation of three points), thread, ellipse and parabola and rigid tapping.
26-Auto chamfering
27-Thread
28-Common thread (follow the spindle)/rigid thread
29-Single-headed/multiple thread of straight, taper and terminal surface in metric system/inch system, equal and variable pitch thread
30-Thread retraction length, angle and speed characteristics can be set
31-Thread pitch: 0.01mm~500mm or 0.06 tooth/inch~25,400 tooth/inch
32-Acceleration and deceleration function
33-Cutting feeding: Linear type or index type is selectable.
34-Rapid traverse: Linear type or S typeThread cutting: Linear type or index type is selectable.
35-The starting speed, finishing speed and time of acceleration and deceleration are set by the parameter.
36-Spindle function
37-Analog voltage 0V~10V output in two channels, support two-spindle control.
38-Spindle encoder feedback in one channel, the resolution of spindle encoder can be set(100p/r~5000p/r).
39-The transmission ratio between encoder and spindle is: (1~255): (1~255)
40-Spindle speed: It is set by S code or PLC signal, the speed range is 0rpm~9999rpm.
41-Spindle override: Total 8 levels: 50%~120%, real-time adjusting
42-Spindle constant surface speed control
43-Rigid tapping
44-Tool function
45-Tool length compensation
46-Tool nose radius compensation (C type)
47-Tool wearing compensation
48-Tool life management
49-Method of setting tools: Tool-setting in fixed position, trial cutting tool-setting, return to reference point, auto tool-setting
50-Tool offset executing mode: Rewriting coordinate mode, tool traverse mode
51-Precision compensation
52-Backlash compensation
53-Pitch error compensation in memory type
54-PLC function
55-PLC program in two levels, maximum 5,000 steps, the refresh cycle of the 1st level program: 8ms
56-PLC program communication download
57-Support PLC warning and PLC alarm
58-Support many PLC programs (maximum 16), the current running PLC program can be selected
59-Basic I/O: input in 40 points/output in 32 points
60-Man-machine interface
61-7.4″large screen LCD, the resolution is 234×480
62-Display in Chinese, English, Spanish or Russian, etc
63-Display in two-dimensional tool path
64-Real-time clock
65-Operation management
66-Operation mode: Edit, auto, MDI, mechanical zero return, MPG/single step, manual, program zero-return
67-Operation authority of multiple-level management
68-Alarm record
69-Editing program
70-Program capacity: 25M, 10,000 programs (including subprograms, macro programs)
71-Editing function: program/block/characters research, rewriting and deleting
72-Program format: ISO code, support macro command programming in sentence type, programming of relative coordinate, absolute coordinate and hybrid
coordinate.
73-Calling program: Support macro program with parameter, subprogram nesting of 4 layers.
74-Community function
75-RS232: Files of part program and parameter, etc can be transmitted in two-way, support PLC program, serial ports of software upgrade.
76-USB: File operation and file directly processing in flash disk, support PLC programs, flash disk of software upgrade.
77-Safety function
78-Emergency stop
79-Hardware travel limit
80-Software travel limit
81-Data restoring and recovering
Certificate
- ISO9000
Main Products
cnc controller, cnc system, ac servo motor and driver