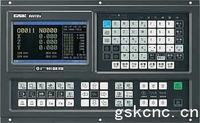
GSK983M
GSK983M
GSK983M is a high cost-performance and high reliable CNC developed especially for high speed, high precision and high efficient machining. Due to the applied high speed micro processor and high speed and precision servo system as well as sufficient CNC and high speed PLC functions, the machining efficiency has truly realized a higher standard.
High precision machining
The high precision and high resonance position control has been realized by high performance position closed loop control chip and high precision position detecting components.
The mechanical errors in transmission chains such as pitch error of ball screw can be remedied by pitch memory error compensation.
Feedrate override can be automatically adjusted in the corner contour machining.
High speed machining
When the system resolution is 1μm, the highest feedrate can reach 240m /min which is suitable for the control of milling press, MCs, engraving machines and super precision machine tools. The continuous high speed machining of micro block is realized by the distributed processing of multi-high speed CPU. The super processing capability of 1000 instruction words per second is especially suitable for the machining of high speed mould, auto parts and the control of woodworkers and laser machines.
High speed DNC functions
The specially developed high speed DNC buffer interface realizes the high speed DNC machining by the connection to PC or U disk at the baud rate as high as 115200 .
Sufficient control functions
It has the functions of maximum 5 feeding axes plus 1 spindle control, cutting tools life management, scaling, coordinate system rotation, complex canned cycle, background editing, graphics display and special user macro program that can easily carry out some special machining.
Powerful built-in PLC
The built-in sequence control for machine and the large PLC capacity for peripherals have greatly simplified the strong power design.
PLC-A 2000 steps PLC-B 12000 steps
Smart CNC
It adopts the latest high integral FPGA, CPLD chips and surface sticking adornment techniques which greatly reduces the dimensions of the control unit. And the LCD displayer adopted realizes the thin model of display unit.
Module I/O
The module design adopts I/O unit which can be paralleled by requirement with maximum (input/output) points are 192/128. It can be fixed on the standard DIN rail to directly drive the load such as contactor, which makes the strong power design much simple and the space taken up is much more reduced.
The wires from CNC to strong power plate are much more saved through the connection of the high speed serial communication ports with CNC.
The machine operation panel
It has maximum 64 mechanical keys with a LED indicator for each. Their function specified by PLC programming and also they can correspondingly connect the switches of feedrate override, spindle override, MPG override and coordinate axis.
Separating structure:
Connect CNC by the high speed serial communication ports to save the wire.
GSK983M is a high cost-performance and high reliable CNC developed especially for high speed, high precision and high efficient machining. Due to the applied high speed micro processor and high speed and precision servo system as well as sufficient CNC and high speed PLC functions, the machining efficiency has truly realized a higher standard.
High precision machining
The high precision and high resonance position control has been realized by high performance position closed loop control chip and high precision position detecting components.
The mechanical errors in transmission chains such as pitch error of ball screw can be remedied by pitch memory error compensation.
Feedrate override can be automatically adjusted in the corner contour machining.
High speed machining
When the system resolution is 1μm, the highest feedrate can reach 240m /min which is suitable for the control of milling press, MCs, engraving machines and super precision machine tools. The continuous high speed machining of micro block is realized by the distributed processing of multi-high speed CPU. The super processing capability of 1000 instruction words per second is especially suitable for the machining of high speed mould, auto parts and the control of woodworkers and laser machines.
High speed DNC functions
The specially developed high speed DNC buffer interface realizes the high speed DNC machining by the connection to PC or U disk at the baud rate as high as 115200 .
Sufficient control functions
It has the functions of maximum 5 feeding axes plus 1 spindle control, cutting tools life management, scaling, coordinate system rotation, complex canned cycle, background editing, graphics display and special user macro program that can easily carry out some special machining.
Powerful built-in PLC
The built-in sequence control for machine and the large PLC capacity for peripherals have greatly simplified the strong power design.
PLC-A 2000 steps PLC-B 12000 steps
Smart CNC
It adopts the latest high integral FPGA, CPLD chips and surface sticking adornment techniques which greatly reduces the dimensions of the control unit. And the LCD displayer adopted realizes the thin model of display unit.
Module I/O
The module design adopts I/O unit which can be paralleled by requirement with maximum (input/output) points are 192/128. It can be fixed on the standard DIN rail to directly drive the load such as contactor, which makes the strong power design much simple and the space taken up is much more reduced.
The wires from CNC to strong power plate are much more saved through the connection of the high speed serial communication ports with CNC.
The machine operation panel
It has maximum 64 mechanical keys with a LED indicator for each. Their function specified by PLC programming and also they can correspondingly connect the switches of feedrate override, spindle override, MPG override and coordinate axis.
Separating structure:
Connect CNC by the high speed serial communication ports to save the wire.
Certificate
- ISO9000
Main Products
cnc controller, cnc system, ac servo motor and driver