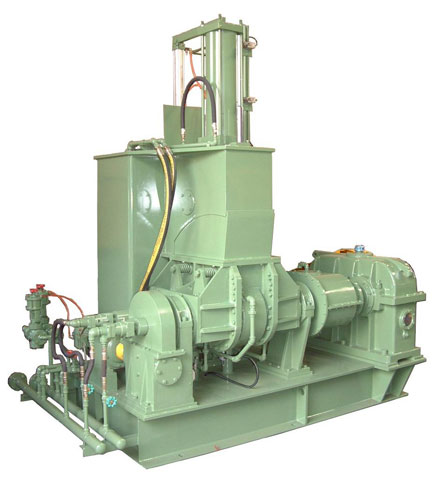
This mixer has most suitable compounding & kneading application for all kind of Rubber, Plastic and Chemical material.
Enhanced Dispersion
In the past twenty years the Dispersion Mixer has become the most commonly used type of mixer in the rubber and plastics industries. The Kneader mixer with its uniquely designed rotors, rotor blades, mixing chamber and pressure lid allows for thorough material flow and controlled shear mixing within the mixing chamber. This intensive mixing achieves a uniform compound mixture with exceptional dispersion of materials.
Unitized Design
The compactly unitized Dispersion Mixer combines all the mixer components on a common bed. This structure simplifies installation and can be easily re-located.
Easy Cleaning
One of the most important features and advantages of the Dispersion Mixer is its easy cleaning and color change capability. The tilting action of the mixer chamber makes this possible and gives full access to all material contact surfaces for easy and complete cleaning.
Dust Stop Seals
A special high temperature oil-less dry mechanical seal is used between the mixing rotor and chamber. This seal minimizes wear and material leakage as well as eliminating compound contamination with lubricating oils. The simplified seal design allows for quick and easy seal changes.
Mixing Contact Surfaces
The Kneader Dispersion Mixers are available with a variety of surface treatments for the toughest compounds. From mixing silicones to ferrous compounds, treatments include hard chrome, stainless steel and specialty carbide finishes.
Optional Equipment
Auto Weighting System, Recorder(time & temperature), PLC Control, Touch Screen Panel, Inverter Drive Motor, Disk Brake, Chamber Safety Pin lock, All our models have CE certificate
Enhanced Dispersion
In the past twenty years the Dispersion Mixer has become the most commonly used type of mixer in the rubber and plastics industries. The Kneader mixer with its uniquely designed rotors, rotor blades, mixing chamber and pressure lid allows for thorough material flow and controlled shear mixing within the mixing chamber. This intensive mixing achieves a uniform compound mixture with exceptional dispersion of materials.
Unitized Design
The compactly unitized Dispersion Mixer combines all the mixer components on a common bed. This structure simplifies installation and can be easily re-located.
Easy Cleaning
One of the most important features and advantages of the Dispersion Mixer is its easy cleaning and color change capability. The tilting action of the mixer chamber makes this possible and gives full access to all material contact surfaces for easy and complete cleaning.
Dust Stop Seals
A special high temperature oil-less dry mechanical seal is used between the mixing rotor and chamber. This seal minimizes wear and material leakage as well as eliminating compound contamination with lubricating oils. The simplified seal design allows for quick and easy seal changes.
Mixing Contact Surfaces
The Kneader Dispersion Mixers are available with a variety of surface treatments for the toughest compounds. From mixing silicones to ferrous compounds, treatments include hard chrome, stainless steel and specialty carbide finishes.
Optional Equipment
Auto Weighting System, Recorder(time & temperature), PLC Control, Touch Screen Panel, Inverter Drive Motor, Disk Brake, Chamber Safety Pin lock, All our models have CE certificate
Features
.Easy cleaning, dust stop,price wiseMain Products
Waste plastics cleaning and recycling plant for PP, PE, PVC, PET, etc.