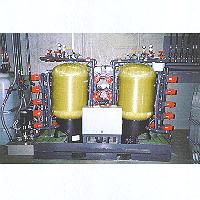
Bioponic International's MR3 technology combines high-affinity metal capture, metal refining, waste decontamination, and water purification into a single integrated system. This new and highly efficient technology is used to separate and recover valuable metals from industrial waste and other sources, such as mining tailings and mineral reserves. The MR3 process represents a breakthrough in metals removal and reclamation, as it selectively extracts individual metals and separates them into high purity fractions using a cost-effective passive process. The MR3 System generates little or no waste of its own, and thus is environmentally beneficial and economically sound. Furthermore, the low capital, operational, and maintenance costs, in conjunction with innovative state-of-the-art engineering, can mean profits from applications previously considered cost-prohibitive. By separating and extracting individual metals for sale, the process convents environmentally toxic liabilities into non-hazardous, profitable assets. General overview: Metal contamination in harbors, lakes and oceans; sewage sludge; mining tailings; polluted soils; acid mine water; industrial wasters; photographic rinse waster; fly ash; and electric arc furnace dust-are only some examples of existing conditions that represent environmental problems of massive proportions. However, in many instances these potential economic disasters contain commercially attractive loads of valuable metals due to their high concentration. At the other end of the concentration spectrum, very minute amounts of radio-nuclide metals, e.g., cesium-137 (Cs-137) and stronitium-90 (Sr-90), the by-products of nuclear electrical power and military bomb production, present an even greater health hazard to the world's human and animal populations due to their extreme toxicity even in minute amounts. These highly radioactive wastes are stored in very dilute solution in large volumes of water at various sites throughout the world. The MR3 technology can help solve many of these and other problems from one end of the concentration spectrum to the other. The MR3 solution consists of a continuous operation in which several process steps, i.e., selective capture, purification, and concentration of individual metals removed from industrial, radioactive or mining wastes, have been integrated into one automated modular treatment plant. The MR3 plant uses sophisticated and highly innovative engineering and special MR3 ion-exchange media of unprecedented affinity, selectivity and density to economically remove and simultaneously purify almost any metal from aqueous solutions. It operates efficiently with metal concentrations of over 20,000 parts per million (ppm) to less than one part per billion (ppb). Water has been successfully cleaned of radio-nuclides (e.g., Sr-90 and Cs-137) to undetectable levels, even with staring concentrations as low as parts per trillion. In the MR3 process, hazardous metals in soils, tailings, sediments, sludges or ashes are brought into solution and thus moved from their solid state into an aqueous state in the form of slurry. The solid materials are then separated from the metal-laden liquid as the solution passes through metal recovery modules where each module selectively removes its target metal from the mixed metal stream. Each separated metal is then processed individually into a non-waste, metal product (e.g., ferric sulfate [Fe2(SO4)3] for drinking water purification; zinc sulfate [ZnSO4.H20] for fertilizer; and copper sulfate [CuSO4.H20] for algaecide or animal feeds). In instances where the quantity of metal may be of no commercial interest (e.g., metals from most contaminated soils), all toxic metals may be simultaneously removed from the water by a single MR3 module. Where a metal-contaminated water is the starting material and thus already in an aqueous state, the water with its metal load enters the MR3 process, and the cleaned effluent water can be introduced directly into the environment or used for other purposes. The water used internally as a metal carrier in the MR3 process is reused repeatedly. The repeated re-use of process water and the fact that the process generates little or no waste of its own contribute to the MR3 System's being environmentally beneficial and economically sound. Background information: During the early 1980s, Dr. Irving W. DeVoe, then a Professor of microbiology in the Faculty of Medicine at McGill University in Montreal, Canada, was actively engaged in research related to the extremely efficient mechanisms employed by microbial and animal cells, in capturing and transporting required nutrient metals. Several metals, such as calcium, chrome, cobalt, copper, iron, magnesium, manganese, nickel, potassium, selenium, sodium, and zinc, are essential nutrients for the maintenance of life in all cells, but some of these metals can be highly toxic if they are not maintained within a specific range of concentration. Though millions of years of evolution, life forms have developed specialized molecules with very high affinity and selectivity for certain of these require metal nutrients. For example, such selective molecules may be released by microbes to capture the relatively insoluble metal iron. As Dr. DeVoe's research progressed, it became evident that the use of special molecules by biological systems to capture various metals at extremely high affinities should provide a useful model for the synthesis of compounds which could be used to capture selected metals from water or other solutions with similar efficiency. The first such molecules so designed by Dr. DeVoe's research group were those with a high affinity and selectivity for iron. Such iron-loving molecules were then made into an insoluble metal-capturing medium by attaching them to a variety of polymers such as glass, nylon, polystyrene and other organic and inorganic materials. By placing these particulate media in glass columns and passing solutions over them, it was possible to remove only the iron from a variety of solutions, some as complex as sea water. The technology for the specific removal of iron from various solutions has a road range of applications in biotechnology. All spoilage micro-organisms must obtain iron as an essential growth nutrient, and thus a product devoid of iron cannot support the growth of spoilage microbes. In many instances, such microbial growth is undesirable and results in spoilage, fouling and dangerous microbial contamination of commercially valuable products ranging from pharmaceuticals and food products to cosmetics and non-food beverages. This generally necessitates either the addition of various preservatives to inhibit the growth of spoilage microbes or the preparation of sterile products. The latter, however, are susceptible to spoilage once they have been opened, and the use of preservatives has been found to produce undesirable side effects. Iron is not a necessary component in most of these products, but amounts of iron sufficient to support microbial growth are nevertheless generally present in such products. This is not due to the purposeful addition of iron to products during their manufacture but rather to the chance addition of small amounts of iron which are present as contaminants in even high quality components used in the manufacture. To date, the pharmaceutical, cosmetic, biotechnological and food/beverage industries have not been aware of the potential grains from the specific removal of iron from their products. The results obtained from early experiments conducted by Dr. DeVoe's team were dramatic. When iron was removed specifically from solutions, microbes were unable to grow and deterioration or spoilage was arrested or significantly reduced. This was the first of a series of successful applications using the basic iron-removal technology. Continuing experimentation showed that new molecules and new media could be designed and synthesized with high selectivity for other metals. The synthesis of these media and success of their initial testing opened up an even broader area of applications ranging from the efficient capture of radioactive metals to the capture of toxic metals from industrial waste effluents. It soon became evident that the ability to target and remove specific metals constituted a technological breakthrough of major proportions. Development of MR3 media: To date approximately thirteen MR3 media have been developed, synthesized, and successfully field-tested. They have all proven to display excellent capacities for metal capture, each being specific to an individual metal or group of metals. These MR3 media have high degrees of specificity and affinity specifically for: aluminum, arsenic, cadmium, cesium, chromium, cobalt, copper, gold, iron, lead, magnesium, manganese, mercury, molybdenum, nickel, plutonium, selenium, silver, strontium, thorium, titanium, uranium, vanadium, and zinc. The media are non-toxic and are far more efficient in capturing metals from water than are the conventional and commonly used ion-exchange materials. Moreover, metal capture from MR3 media is highly selective, which represents a distinct advantage over conventional ion-exchange resins. In instances where it is desirable to remove more than one metal, more than one metal-specific column may be used in a series. With some media, it is possible to broaden their specificity by chemical modification or special conditioning. As a result, a number of different metals can be removed from solutions simultaneously. The MR3 System can also be used in conjunction with conventional ion-exchange materials when the simultaneous use of both high and low capture efficiencies can produce the intended results. The design features and characteristics originally sought have attained with respect to a relatively large selection of media useful for the separation of a broad spectrum of metals from solution. The requirements originally set forth for affinity, specificity, selectivity, performance, stability, regenerability, capacity, toxicity and cost-efficiency have in all cases been met successfully and in many instances have been surpassed. Detailed description of the MR3 process: The MR3 process divides readily into three stages: Stage one - Front End; Stage Two - Metal Separation; Stage Three - Metal Products. Stage One prepares the metal - bearing starting material (feed stock), whether in a solid or liquid state, for injection the MR3 system, by putting the metals into the optimal aqueous form for continuation of the MR3 process in Stage Two. The composition of the starting material determines the physical plant of Stage One. The MR3 system adapts well to feed variability: feed stocks may consist of metals in a solid matrix such as ore, tailings, sludge, ashes, soils, and harbor sediments, or in an aqueous form, such as plating baths or rinse water, galvanizing baths, acid mine water, etc. Such liquid feed stocks require little more than a surge tank in Stage One, whereas solid feed stocks require equipment suitable for the liquid extraction of the target metals, separation of the solids from liquid extracts, and holding of the extracts for subsequent processing in Stage Two. The operation of the Stage One physical plant is controlled by an MR3-automasted electronic control system which maintains the movements of slurries, introduces reagents, and controls timing, temperature, and pH throughout the plant. Process labor requirements are minimal. Stage One adapts to a variety of job sizes, from small jobs of several tons per day to those of thousands of tons of solid feed stock per day. In instances where feed stocks are already in an aqueous state, thousands of GPM (gallons per minute), which translates into millions of gallons per, can be processed with a relatively small plant. Even smaller plants are available for processing minimal GPM. Input water may concentrations of over 20,000 parts per million (ppm), or less one part per billion (ppm). Stage Two-Metal Separation: This stage, the heart of the MR3 system, passively separates individual metals into highly pure forms. The extract from Stage One is pumped continuously into module one of Stage Two. There, as the first target metal is removed, the extract (minus the first target metal) continues until all the desired metals have been removed sequentially from the extract water. A single metal separation module consists of several enclosed pressure tanks, each containing a special medium exhibiting a higher affinity for its target metal than for others. By this means, a module selects its individual target metal from among many others in the stream, making the sequential removal of selected metals possible. Whereas Stage One is operational as a "continuous batch" system, Stage Two is a continuous steady-state operation, where water flows continuously through the series of modules, thus permitting large daily inputs through a relatively small plant. The target metals, each having progressively accumulated in their respective modules at rates independent of one another, are removed from their binding sites on the medium at appropriate intervals as a highly pure, single-metal salt, e.g., zinc sulfate (ZnSO4) or copper sulfate (CuSO4), for further processing in Stage Three. In addition to producing single-metal side-streams, the main stream through the module becomes progressively pure as it proceeds through each metal-separation module in Stage Two. By the time water exits Stage Two, it typically meets environmental requirements for direct discharge. However, in many instances where feed stocks are solid materials, up to 90% of this effluent water is conserved for recycling back through the process with only 10% remaining as a blow-down of high quality water for discharge. Since the MR3 process removes heavy metals from the metal-extract stream to undetectable concentrations, i.e., below 0.01 ppm (or in the instance of radio-nuclides, to concentrations millions of times lower), it is extremely unlikely that they would appear in the blow-down. In summary, Stage Two selectively pulls target from the aqueous metal extract stream and turns them out separately as single-metal salt solutions. Typically, metals in these slat solutions will have a purity exceeding 99%, a noteworthy accomplishment for a first purification cut, even from concentrations higher than 30,000 ppm. Stage Three-Metal Products: The physical plant of Stage Three is determined by the desired final product or disposal plan of the user. After each metal I is separated in Stage Two, Stage Three can transform these metal salts into products for sale. Because of their high purity, separated copper or zinc, for example, may be taken out of solution by vacuum evaporation. Alternatively, the metal in sulfate salts can easily be converted to its oxide form, or taken by Electro-reduction to its metallic form. Metal sulfate salts have immediate markets as plant fertilizers and animal feed components. For example, zinc sulfate, the largest commodity used to male fertilizer, is in constant demand. Manganese and magnesium are also readily marketable as both sulfates and oxides. Even the ubiquitously present iron is in demand in the market as iron sulfate, a product inexpensively produced with the MR3 process. Municipal and industrial water treatment consumes large quantities of this salt, customarily delivered in rail car quantities in concentrated liquid from. In other instances where quantities of input metals are small and do not warrant their conversion to specific metal products for sale, all contaminating metals may be captured in a single module in Stage Two; in these case Stage Three is not necessary. In summary, Stage Three processes the output Stage Two, i.e., single-metal streams. Both Stage One and Stage Three are designed to meet the specifications of the end-user, whereas Stage Two remains relatively constant, regardless of the mission of the plant. Technical specifications: The MR3 technology functions over a pH range from 1 to 14 and a temperature range from 5 Celsius to 95 Celsius. It yields a purity exceeding 99% of the target ion, such that the output is immediately salable with no further processing. It works over a concentration range from 1 molar to parts-per-trillion, yielding removal ratios of 40,000 to 10 million, even in the presence of high concentrations of competing ions. The media capacity is on the order of 14 moles per cubic foot. Metal separated to date include: aluminum, arsenic, cadmium, cesium, chromium, cobalt, copper, gold, iron, lead, magnesium, manganese, mercury, molybdenum, nickel, plutonium, selenium, silver, strontium, thorium, titanium, uranium, vanadium, and zinc. Foreign markets for many of the target industries described above are particularly ripe for the MR3 technology because of decades of irresponsible policies allowing the indiscriminate release wastes into the environment. Accelerating further the markets in both Eastern and Western Europe is the advent of new legislation which will prohibit the dumping of hazardous wasters into landfills and the transport of these wastes outside their country of origin. In Switzerland, for example, new legislation has already been passed, putting companies who are active in the metal refining and waste hauling industries on serious notice. Bioponic International foresees on the horizon numerous potential business opportunities as a result of the changing worldwide concerns regarding environmental problems.
Features
- During the development of the MR3 media, the following required features and characteristics have been established for optimal performance:
- Affinity: very high capture efficiency in solutions containing low metal concentration.
- Specificity and Selectivity: the ability to capture specific metals while ignoring others present in the same medium.
- Performance: high flow rates with freedom from swelling, shrinking, and compaction due to hydrostatic or osmotic pressure.
- Stability: strong resistance to harsh chemical and physical treatment.
- Regenerability: easy displacement of the captured metals from charged media, resulting in metal concentration, high-volume reduction factors, and re-use of free media.
- Capacity: ability to capture substantial amounts of metal per unit of media while still maintaining high capture efficiency.
- Toxicity: freedom from toxicity, there being no addition of trace toxic components to the treated solution.
- Cost-efficiency: low production costs minimized further by media regenerability.
- Potential applications: The MR3 technology can be used to extract and recover metals from a vast range of sources, originating as both solid and aqueous states. Specific examples of applications include:
- Water purification, metal reclamation, and refining from metal-laden industrial water or sludge waste.
- Water purification and metal reclamation from metal-laden mine water.
- Metal reclamation (including gold) from mining tailings.
- Cleaning sewage sludge and sewage sludge sludge ash.
- Cleaning fly ash and bottom ash.
- Cleaning contaminated soils, including silt and clay fractions.
- Cleaning ground water of heavy metal contamination, including chromate (Cr-6).
- Cleaning harbor and lake sediments (can work in conjunction with dredges).
- Recovery of metals and water from plating rinse waters.
- Recovery of metals from industrial hydroxide sludge from the metal finishing industry.
- High-affinity capture of low concentrations of radio-nuclides (e.g., Cs-137, Co-60, Sr-90, Pu) from water.
- Recovery and purification of gold and other precious metals from ore and placer.
- Recovery of individual metals from process residuals (e.g., flue dusts).
- Recovery of individual metals from bag-house contents (e.g., electric arc furnace dust, etc.).
- Recovery of individual metals from slags and cinder.
- Selective recovery of the oxidized iron ion, leaving the non-oxidized ion, from picking baths used in the auto industry.
- Selective removal of iron from Electro-galvanizing baths to greatly prolong bath life.
- Removal of extremely low concentrations of industrial metals from sewage plant outflows.
- Removal and recovery of metals from spent catalysts.
- Removal of metals from waste water of electronics industry (circuit boards, thick films, thin films, wafers).
- Recovery of precious metals from computer junk.
- Metal decontamination of blasting sand used in paint removal from ships, etc., and recycling of the sand.
- Recovery of selenium from agricultural irrigation waters, from water used to wash crude oil, and from waste water from the Xerox production process.
- Selective removal of contaminating iron from any aqueous solution for the prevention of microbial growth.
- Target industries: Bioponic International's targeted market areas for its MR3 technology are identified and represented by the following industries. Data regarding the number of specific industrial sites for each market area was compiled from the Phone Search USA 3.0 CD-ROM Directory (DeLorme: Yarmouth, Maine).
- Metal finishing and plating: These industries generate enormous amounts of hydroxide sludge and other metal wastes in the metal finishing and plating processes. Bioponic International has identified more than 10,000 separate metal finishing or plating sites in the U.S. There are also tens of thousands of additional sites estimated that conduct metal finishing or plating operations solely for their own in-house purposes.
- Electronics: The electronics industry generates significant amounts of metal wastes in the manufacturing of circuit boards and other electronics components. There are an estimated 1,500 circuit board manufactures and 650 electronics components in the U.S.
- Textiles and paints: These industries use and generate as waste large amounts of toxic metals in the production of dyes and paints. There are more than 1,500 industrial textile process and manufacturing sites estimated in the U.S. as well as numerous paint manufacturing sites.
- Incineration: The incineration industry generates huge amounts of valuable metal wastes which are present in the smoke and ash from industrial and municipal incinerators.
- Steel: The electric are and other furnace used in the steel industry generate significant amounts of metal wastes. There are more than 1,250 industrial steel furnace sites estimated in the U.S.
- Mining: The mining industry provides an almost inexhaustible source of metals for the MR3 process in the form of ore, placer, and tailings. Concerning the mining of precious metals specifically, the MR3 technology's ability to separate gold and silver from black sands and other concentrates represents significant opportunities for Bioponic. There are more than 650 mining companies estimated in the U.S.
- Water purification: Although not at present a primary source of salable metals for Bioponic International the water purification industry should provide many business opportunities for the MR3 technology, as the presence of toxic and unwanted metals is a growing vital concern to all those served by this industry.
- Soil remediation: Situations where the ground is contaminated by the leading of toxic metals waste stockpiles (e.g., mining tailing, junkyards, landfills, etc.) into the soil below offer huge potential metal recovery projects for Bioponic. Due to the massive volume of soil contaminated by metals, this industry represents literally decades of continuous work for the MR3 technology in the U.S. alone.
- Harbor and river sediment remediation: Harbors and rivers all over the planet have been severely contaminated from metal refineries and other metal waste-producing industries. As much as 30% by weight of the sediments from contaminated harbors and rivers consists of metals. The MR3 technology effectively cleans the slit and clay fractions, in which 95% of the metal contamination in the sediments exists.
- Surface water cleanup: Countless ponds, lakes, and other inland bodies of water have been contaminated from the industrial dumping of metal wastes into the rivers and streams which feed them.
- Ground water remediation: Toxic metal from contaminated soils leach natural aquifers which must be cleaned before these underground bodies of water can be used as sources of drinking water.
- Radioactive waste: The nuclear power and weapons production industries continue to generate incredible amounts of deadly radioactive metal wastes, and classic methods of isolating and removing the radioactive metal ions from the huge quantities already stockpiled have not been successful to date.
- Photography and x-rays: The photographic and medical imaging industries represent opportunities for MR3 silver-recovery on a grand scale, as tremendous amounts of silver are present in warehoused x-ray films and in photographic bleach/fix solutions and rinsewaters. There are more than 25,000 photofinishing locations and 9,000 x-ray testing labs estimated in the U.S.
- Medical: The medical and pharmaceutical industries should prove to be valuable potential market areas for the MR3 technology. There are more than 75,000 hospitals estimated in the U.S.
- Metal waste resources: The following types of metal-laden wastes will provide Bioponic with metal-removal opportunities and/or sever as potential resources for recovery and sale of metals:
- Hydroxide sludges from the metal finishing, aircraft, mining, electronics, and metal smelting industries.
- Fly ash and bottom ash from the incineration, utilities, and sanitation industries.
- Electric arc furnace dust (EAFD) from the steel industry.
- Radioactive waste from the nuclear industry.
- Slags and cinder from the chemical industry.
- Metal catalysts from the chemical industry.
- Chromium from the tanning, metal finishing, and smelting industries.
- Acid mine water and tailings from the mining industry.
- The MR3 system is ideal for selectively extracting valuable metals for recycling and resale from a large number of sources in the following areas: metal finishing and plating, electronics, textiles and paints, incineration, steel, mining, water purification, soil remediation, harbor and sediment remediation, surface water clean-up, ground water remediation, radioactive waste, photographs and X-rays, medical.
Main Products
MR3 metals recovery system, airponic growing system