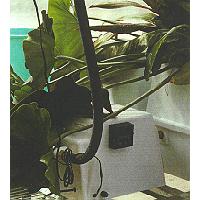
Bioponic International offers Airponic Growing Projects, which can accelerate and increase food and horticultural production, expand the scope of plant research and provide global reforestation and reclamation projects with high volumes of genetically sound seedlings for out-planting. The Airponic Growing System is a high-technology growing method that excels in large-scale projects requiring high yield plant production, phytopharmaceutical research and development or in reforestation and land reclamation projects. For environment reforestation or reclamation projects: The Airponic Growing System is designed to be the basic growing technology for any large-scale environmental project involving reforestation, land reclamation, erosion control, watershed management or the preservation and replication of endangered plant species. The system has the ability to asexually propagate large volumes of indigenous plant species at a highly accelerated rate; and can be installed in remote growing facilities, on-site in the affected region. The technology allows for the selective propagation and regeneration of superior local cultivars indigenous to the areas designated for replanting by utilizing any remaining cultivars as "Mother Stock". The fact that remaining or neighboring soil may be nutrient poor or ill suited for agriculture does not impair the Airponic regeneration process. The Airponic System eliminates the high project cost of importation and handing of non-indigenous plant material, low plant survival rate and yield, and large scale remote nurseries. For the phytopharmaceutical or research organization: For plant research organizations and phytopharmaceutical growers the Airponic technology can expand its research capabilities in developing phytochemical production. The root zones of Airponically-grown plants are accessible to biochemical manipulation. Specific nutrient and/or chemical precursors can be delivered directly to the root systems free of interference or buffering from soil or other substrate growing media. Plants producing phytochemicals grow fast and more consistently. Users are assured of a constant supply of medicinal plant material in a controlled environment, eliminating dependence upon outside supplies and supplier of raw plant material. Plus, the Airponic technology provides the ability to harvest roots, thus creating a renewable, regenerated supply of root biomes and a potential source of phytochemicals. For the greenhouse or nurseryman: Airponic growers can experience significant increases in their production profits over previous earnings from soil-based growing. Plants produced in Airponic Growing Systems normally grow at a highly accelerated rate, many times faster and with superior quality than other growing methods. Airponic growing provides horticultural producers with a competitive advantage over those using conventional methods. Many food crops, foliage, flowers and seedling trees grow fast, and in less space, than with other methods. By accelerating the plant propagation cycle, the Airponic System increases the per square foot yield of the modern greenhouse, often producing several harvestable crops in the time usually required for a single crop. Profits per square foot of greenhouse space can be increased significantly. Airponic growing: Airponics is the method of accelerating the growth of plants in an oxygen-rich environment, without soil, where the plant's root's zone is suspended in a growing chamber and intermittently pulse-misted with a nutrient solution. The company's Airponic technology consists of both the "hardware" and "software" aspects of the Airponic Growing System. The hardware is made up of a proprietary assembly of growing chambers with spray arm manifolds, Hydrocontrols, and digital timers and Plantcycle equipment. The software consists of trade secret nutrient and chemical formulas, plus application know-how and methodology. Airponic production capacity: Each Airponic Growing System consists of a set number of Growing Chambers with a matching Plantcycle System designed to process and recycle the nutrient solutions efficiently to reach maximum production. The propagation production capacity of the system is keyed to plant species selected and the diameter of its cutting. Each Growing Chamber contains 161 support holes, and each hole has the capacity to hold from one to five cuttings (depending upon cutting diameter). Plant species have differing propagation cycles in the Airponic System, with most species having either a 7 day, 14 day, or 30 day cycle (propagation cycle = the number of days it takes to produce a root system on an unrooted cutting sufficient to enable it to be transplanted to soil and survive under normal conditions). The maximum annual plant production capacity per AGS Growing Charber for the three most common propagation cycles is illustrated on the following page. High yields = High profits: The increase in growing profits per square foot of greenhouse space due to accelerated propagation cycles is illustrated by the following table where a grower's annual profit using an AGS Model 10 is compared to his profit from the same amount of greenhouse space using conventional soil methods. This table compares the production efficiency and increased profit capabilities of the Airponic System Model 10 (100 Growing Chambers) against conventional sand culture, soil or bed methods. The numbers used represent an average sample for a crop of ground cover (such as Ivy) or foliage plants (such as Pothos) on a 14 day Airponic cycle using 3 cuttings per hole. The AGS product line: The Company offers a product line in a series of modular Airponic Growing Systems. Each model is designed as a complete life support vehicle for accelerating the plant's propagation and growth cycle. It uses a closed-loop process, which delivers the nutrient solution to the plant root zone in a pulse-mist application inside a Growing Chamber and then recovers and recycles the solution via the Plantcycle System - a multi-stage bioactive filtration apparatus. Each Airponic Growing System consists of a set number of Growing Chambers, Hydrocontrols with Digital Timers, and the Plantcycle System. The flexibility of the Airponic "software" adds to the System's desirability for reclamation and preservation projects. Many species are difficult or close to impossible to propagate outside of their natural state due to complex microclimate balances and their effect on the stratification and germination of seeds. By adjusting the nutrient parameters and spray sequences within the System, the user is able to replicate the exact nutrient profile for each species and thereby substantially increase the plant regeneration success rate.
Plant Cutting Per Hole | Plant cutting per hole | Plant cutting per hole | Plant cutting per hole | Plant cutting per hole | Plant cutting per hole |
---|---|---|---|---|---|
Propagation cycle | 1 | 2 | 3 | 4 | 5 |
7 Day (52Cyc/yr) | 8,372 | 16,744 | 25,116 | 33,488 | 41,860 |
14 day (26Cyc/yr) | 4,186 | 8,372 | 12,558 | 16,744 | 20,930 |
30 day (12Cyc/yr) | 1,932 | 3,864 | 5,796 | 7,728 | 9,660 |
Specifications
- Production area (Sq. Ft.):
- Conventional: 640
- Airponic: 640
- # of crops annually:
- Conventional: 8
- Airponic: 26
- # of plants per Sq. Ft.:
- Conventional: 36
- Airponic: 75
- Plant loss (% annually)
- Conventional: 40%
- Airponic: 20%
- Annual yield (# of plants):
- Conventional: 110,592
- Airponic: 1,004,640
- Production cost (per plant):
- Conventional: $.10
- Airponic: $.09
- Wholesale price (per plant)
- Conventional: $.15
- Airponic: $.16
- Annual Profit:
- Conventional: $16,589
- Airponic: $160,742
- Model No.1
- No. of growing chambers: 10
- Annual plant production: 100,000
- Greenhouse size (Sq. Ft): 720
- Model No.2
- No. of growing chambers: 20
- Annual plant production: 200,000
- Greenhouse size (Sq. Ft): 1,080
- Model No.5
- No. of growing chambers: 50
- Annual plant production: 500,000
- Greenhouse size (Sq. Ft): 1,440
- Model No.10
- No. of growing chambers: 100
- Annual plant production: 1,000,000
- Greenhouse size (Sq. Ft): 2,160
- Model No.50
- No. of growing chambers: 500
- Annual plant production: 5,000,000
- Greenhouse size (Sq. Ft): 10,800
- Model No.100
- No. of growing chambers: 1,000
- Annual plant production: 10,000,000
- Greenhouse size (Sq. Ft): 21,600
- Model No.500
- No. of growing chambers: 5,000
- Annual plant production: 50,000,000
- Greenhouse size (Sq. Ft): 108,000
- Model No.1000
- No. of growing chambers: 10,000
- Annual plant production: 100,000,000
- Greenhouse size (Sq. Ft): 216,000
- Annual plant production is calculated based on one growing chamber producing three (3) plant cuttings per hole, x 161 holes, x the number of Growing Chamber, x 26 cycles per year (the average propagation cycle), with an average annual loss rate of 20%.
- Note: the possible number of cuttings per hole will vary according to species and cutting diameter.
Features
- Airponic advantages over other growing methods include:
- Quicker Propagation Time-Accelerated rooting times for most species-many plant cuttings root in a matter of days.
- Increased Yield-More healthy plants per square foot. A faster propagation cycle allows for the turnover of more plants per year.
- Improved Survival Rate-Plant cuttings placed in the System remains turgid and fresh. Transplant without shock or setback to normal growth.
- Less Disease-Chambers provides a healthy, oxygen-rich growth medium. No substrate media for the spread of disease or pests.
- Energy and Water Efficient- Reduced water costs per plant produced. 100% of the water and nutrients are recycled with minor water loss due to evaporation.
- Compared to Hydroponics and Tissue Culture Methods-See Appendix I.
- Applications for the Airponic Growing technology include:
- Asexual Macro-propagation of softwood and hardwood plant cuttings-plants reproduced asexually from cuttings experience dramatic root growth in less time than traditional propagation methods. The Airponic System will increase yields of most plant varieties and reduce the produced in the Airponic system ready to transplant to soil in six (6) days. Conventional methods may take 45 days.
- Full Term Growth-Efficient full term food and flower production for many species. Airponic production often yields high densities of flower blooms on a weekly basis. Permits the year-round harvesting of fresh herbs (Sweet Basil and Mint) and vegetables.
- Seed Germination-Most plants, including flower and edible plants (Lettuce, Spinach, Cucumbers, Herbs and more) can be grown quickly from seedling germination of 4-5,000 plants per Chamber (6.4 square feet) is possible.
- Enhancement of Botanical Medicines-Nutrients and chemical precursors can be introduced to root systems to promote "biotransformation" of phytochemicals in high-value plants.
- Tissue Culture-Accelerated acclimatization of young tissue culture plants from the rootless Stage 2 to a healthy Stage 4 rooted liner.
- The system components / The Growing Chamber: Plant cutting stems are inserted through and supported by the upper portions of multi-hold Growing Chambers, with which the suspended roots are stimulated by a hydro-atomized nutrient spray pulse within the Chamber. Each Growing Chamber has a surface area of 6.4 square feet and is constructed of thermoformed UV stabilized plastic consisting of the Chamber top with 161 holes for plant insertion and support and the Chamber bottom. Each Chamber bottom has a four spray arm manifold for nutrient solution distribution to the Growing Chamber interior. It also servers to collect the spray solution effluent for recycling. Plant root systems hanging in the oxygenated enclosed environment of the Growing Chamber receive all the necessary nutrients for accelerated growth. Because the root systems do not compete for moisture or nutrients, plant density can be significantly increased at all stages of development. The Growing Chambers are series connected in lines of up to ten Chambers controlled by a single Hydrocontrol with Digital Timer.
- The system components / The Hydrocontrol with digital timer: The nutrient spray sequence is controlled by a Hydrocontol Unit, which uses a variable microprocessor timer to adjust spray duration and intervals, as well as the nutrient uptake into the system. Each individual plant species possesses unique requirements as to spray intervals, duration and nutrient formulae. The flexibility of the System allows for Hydrocotrol adjustment to assure optimum growing results per species and cultivar.
- The system components / The Plantcycle System: Utilizing our innovative Plantcycle System, the nutrient solution for the Airponic process is recycled through a multi-staged bio-active filtration technique which provides for a clean, balanced and stable nutrient solution, and provides for complete nutrient solution reuse with low water consumption. The Plantcycle System consists of four component water recycling elements (the Effluent Station, Filtration Station, Pasteurization Station and High Pressure Substation). The Plantcycle Systems are designed to process the nutrient solution of from 10 to 100 Growing Chambers. The Plantcycle System recycle all water used in the Airponic System. The water is collected System recycles all water used in the Airponic System. The water is collected via the Growing Chamber bottom, filtered, purified and depressurized in a closed loop process which maintains the necessary nutrient, pH and temperature levels. Plantcycle allows near-zero evaporation loss, in addition to controlling the problems of water quality and nutrient balance.
- The system components / The nutrient chemical: The "software" aspect of Airponic plant growing involves the Company's chemical and nutrient formulas. The optimum condition for Airponic plant growth requires specific nutrient formulas for plant propagation and accelerated growing. The Company has developed proprietary nutrient formulas for successful plant growth in the System. These formulas are developed with a multi-stage approach for each species and cultivar with regard to propagation, vegetative growth and fruiting and flowering.
- Airponic Growing Formula (AGF): Developed as a general full-term growing plant nutrition formula for use in the Airponic System, AGF has proven effective for a wide spectrum of plant species. This balanced liquid formula is fully chelated and contains many of the trace elements which are necessary for accelerated plant growth.
- Airponic Rooting Formula (ARF): Developed as a general plant starting nutrient formula for use in the Airponic System, ARF is high in phosphorus and promotes an acidic nutrient solution balance. This liquid formula stimulates root initiation and provides young plant cuttings with sufficient amounts of phosphorus for healthy growth. ARF also contains useful trace elements for accelerated plant growing, and has proven effective on a wide variety of plant species.
- Airponic rooting agent (ARA): A synthetic auxin that acts to promote root development in a biochemically identical manner as naturally produced auxins. The primary component of ARA is indole 3 butyric acid. Auxins are naturally occurring plant hormonses which are found in plant tissue. ARA has been found to stimulate root initiation when applied to the plant. As a result, the growers can speed-up callus formation and subsequent root development on herbaceous and woody plants.
- Dis-Cal: A liquid formula development for cleaning calcium deposits in the Airponic System. Can be used as a solution additive to assist in the plant calcium assimilation.
- Airponic Disinfectant Solution (ADS): A formulated system disinfectant for cleaning and for preventing the building-up of slime mold and fungus in the Airponic System.
- Oxyplus: A formulated non-hypochloride based system disinfectant, which has demonstrated several beneficial secondary attributes. Oxyplus can assist with nutrient solution nitrate stabilization by releasing oxygen radicals into the solution, which bind with nitrogen molecules and allow toxic nitrite molecules to transmute into plant nourishing nitrate molecules.
- The Airponic Project: Bioponic International offers its customers Turn-Key Airponic Project services and support on a worldwide basis for:
- Food Production
- Foliage Plant Production
- Seedling Production
- Endangered Species Preservation
- Desertification
- Medicinal Plant Replication
- Phtochemical Research
- Land Reclamation
- Rainforest Reclamation
- Reforestation
- The Airponic project / Equipment: Each Project includes a modern greenhouse facility constructed on-side and equipped with advanced environmental controls. The greenhouse is monitored and controlled by remote sensors which can be coordinated and adjusted for the optimum conditions for effective plant growth. Each greenhouse is sized to provide ample space for the operation of its AGS Model and Plant handling activities. Every Airponic Growing Project sold by Bioponic International is Turn-Key and includes:
- An AGS Model assemble of Airponic Growing Chambers and Hydrocontrol Units with Variable Digital Timbers.
- A matching AGS Plantcycle System with its component waters recycling, filtration and nutrient processing elements.
- A peripheral equipment package consisting of back-up power generation, water source pre-filtration device, integrated monitoring and alarm system, humidification equipment, spare parts and complete Airponic laboratory test equipment.
- An annual supply of chemical and nutrient formulas designed specifically for the operation and maintenance of the AGS.
- Detailed Operating Manuals governing all aspects of AGS and Plantcycle Systems.
- A custom-sized, steel-framed and environmentally controlled greenhouse. These modern greenhouse feature galvanized steel benches, automatic roof vents, lexan thermos-clear coverings, positive pressure cooling, turbulation fans, augmentative grow lighting, shade cloth, heating system and a computer based controller for environmental management. Each greenhouse is custom designed to house the specific size of AGS Model for the Project.
- The AGS Turn-Key Installation and Training Program, consisting of greenhouse construction on-site; the set-up, installation and testing of the AGS, Plantcycle System and peripheral equipment package; and on-site training of customer personnel to operate, maintain and trouble-shoot all aspects of the Airponic Growing System. This Program has been designed to introduce customer technicians and horticultural experts to the science and technology of Airponic growing, and to train them to implement an Airponic Greenhouse Production facility and bring it to full production. By the time each AGS Model and Greenhouse is delivered and the Installation and Training Program completed, each customer will be well prepared and qualified to operate its AGS plant production facility.
- The Airponic project / Installation and Training Program: Bioponic International stages its Installation and Training Program, scheduling all construction, equipment installation, testing and train. Your personnel will be trained as Airponic technicians with related Airponic skills in: Systems Operation, Systems Maintenance, Crop Production, Greenhouse Management, Horticulture, Crop Programming & Handling, Environmental Control, and Sanitation. Upon the completion of the Greenhouse structure the Airponic Growing System is installed and tested. The Training Program will begin with initial crop production coming within weeks of the integration of the Greenhouse and the Airponic Growing System. Operations of the Airponic Greenhouse Production Facility are normally handled by the customer's Greenhouse Manager and staff, who will be responsible for all aspects of greenhouse operations.
- Operating the Airponic Growing System according to the manuals and operational procedures established by Bioponic International.
- Greenhouse management including maintaining the growing environment to standards established to by Bioponic International, maintaining AGS sanitary procedures to ensure the optimum growing conditions for each crop, and all necessary equipment maintenance and repairs.
- Processing of all plant material grown in the System according to customer production schedules, which includes shipping or potting cuttings and storing them for proper hardening-off prior to sale and delivery.
- Appendixi-Comparative Growing Techniques: In order to understand the effectiveness of the Airponic Growing System it is useful to draw comparisons to other better known agricultural techniques such as hydroponics or tissue culture.
- Appendixi-Comparative Growing Techniques / Hydroponics: Hydroponics is the technique of growing plants in water or utilizing a substrate media in flow of water or nutrient solution. This technique has severe limitations and many growers who have had negative experiences with hydroponics are unaware of the advantages of the Airponic process.
- Asexual Propagation: The first and foremost point in comparing Airponics with hydroponics is that the Airponic System has been designed to accelerate the propagation cycle of plants grown asexually. This has never been possible in the hydroponics in technique. Plant propagation in the Airponic System is a unique feather of the process.
- Water Borne Disease: In Hydroponics the plants come in contact with nutrient solution. It is typical in this technique for water borne disease to run rampant throughout the Hydroponics solution spreading the disease and killing the crop. In the Airponic System the plants do not contact the water solution directly because they are sprayed intermittently while hanging in the air. Therefore they do not transmit disease caused by constant contact with water borne pathogens. In the Airponic System the nutrient solution is captured and processed in the Plantcycle which is a bio-active multi-stage filtration device. This eliminates organic contamination while preserving the nutrient content. Bioponic has development several safe, effective systemic additives (harmless to plants or people) which purify the solution and prevent fungal molds from taking hold in the System environment.
- Toxic Salt Pollution; With the hydroponics technique in order to maintain the level of desired nutrients, chemical salts must be added regularly. Th nutrient salts build up to toxic levels and must be discarded by dumping the entire nutrient solution and starting over. This wasteful process causes distress in plants and is a primary cause of toxic agricultural pollution. Due to the high oxygenation of the nutrient stream, the Airponic System requires 1/10th of the nutrients that are required in hydroponics. All water and nutrients placed in the Airponic System stay in the System to become plants. The System has been designed for maximum efficiency, with no waste. There is never any dumping of the nutrient solution and never a toxic build-up or pollution problem. The System requires a fraction of the nutrients found in hydroponics, providing for a substantial saving in water and fertilizer expense.
- Oxygen Starvation: The hydroponics solution can become severely depleted of oxygen causing oxygen starvation in plants and retarding the growth process. The nature of the Airponic System is based on providing an ultra-oxygenated environment for the growing plants. Oxygen is the key to accelerated plant growth and propagation. Oxygen is provided by the highly atomized mist of the pulsing microprocessor controlled nutrient solution: by the root systems of plants hanging passively in the air in between nutrient pulses; by the action of the Plantcyle system; and by the additive Oxyplus which enhances the growing process.
- Appendixi-Comparative Growing Techniques Tissue Culture: Tissue Culture is the technique of growing plants from the meristematic cellular material of an individual plant. Whereby many thousands of plants of the same genetic make-up can be produced from one plant. This process may be correctly termed micro-propagation whereas the Airponic System may be called macro-propagation. Again, there are several areas of difference in this process, which need to be discussed in order to elucidate the advantages of the Airponic System.
- Technological requirements: Typical tissue culture facilities require clean room environments with difficult to maintain parameters and graduate university level personnel to operate. The technique for operative tissue transfer into the auger medium requires a high level of precision for success and the preparation of the auger and nutrient media must all be accomplished within strict parameters in order to avoid contamination. Tissue culture laboratories must be equipped with sophisticated equipment including microscopes, incubation chambers, autoclaves, etc. It would be difficult for local populations to be integrated as participants into this technology. The Airponic technology requires only a greenhouse type controlled environment for successful utilization. Greenhouse systems are relatively unsophisticated and are easily learned. Since whole plant cuttings will be used for propagation there is no need for a strict clean room environment. However, basic sanitary procedures will be followed. The ease with which the Airponic System can be learned and the fact that the System can coexist in a greenhouse, which is toleration with local environmental conditions, are important competitive features.
- Disease: In the tissue culture environment disease can have a devastation effect. The auger medium, which is the life source for the young cellular material, is also a prime food source for other microorganisms, which in turn contaminate the petri dish containing the plant cells and render them useless. These tissue culture dishes are extremely intolerant of changes in the environment such as temperature, light and moisture, which must be strictly maintained by the laboratory procedures. The Aoroponic System had addressed the disease problem through its Plantcycle System and systemic additives, which promote the health of the plants in the System while elimination contaminating mircro-organisms. This has all been accomplished in a simple format of procedures, which can be easily integrated into maintenance routine.
- The time factor: In order to grow a plant from a cell there is a significant period in which the plant must establish itself through various stages of growth, called in the language of tissue of tissue culture Stage 1, Stage 2, Stage 3, and Stage 4. Typically from Stage 1, where the cell has been placed in the auger medium in the petri dish, to Stage 4, where the plant is ready for placing in a soil media, the time elapsed can run from 18 to 24 months. Even then the result is a very small plant which will take many months or even years to develop into a plant which can be out-planted or is ready for commercial sale. The main feature of the Airplonic System is accelerated propagation from cuttings (macro-propagation). When a suitable cultivar has been selected, the portion of the plant taken for a cutting can vary. Typically a cutting can be from 8" to 24" and will depend on the type plant desired. The process of including a root system to develop can be as short as 2 to 3 days or as long 30 to 45 days, again depending on the type of plant. To achieve a similar plant in size that can be achieved in the Airponic process in weeks can take as long as 3 years with tissue culture.
- Hardiness Factor: Because of factors not completely understood, plants grown from tissue culture lack hardiness and when grown in warm temperatures will tend to droop significantly. This tendency is undesirable in commercial products. If a hardy product is desired it is necessary to grow the tissue culture plants in cool climates to allow a stunting of the plant and subsequent strengthening. Since it is usually not possible to access a cooler climate for tropical plants, the tissue culture creature created commercial product has been deemed undesirable. The Airponoically rooted cutting exhibits excellent hardiness, responds well to transplantation (with almost 100% success) and be grown in any climate.
Main Products
MR3 metals recovery system, airponic growing system